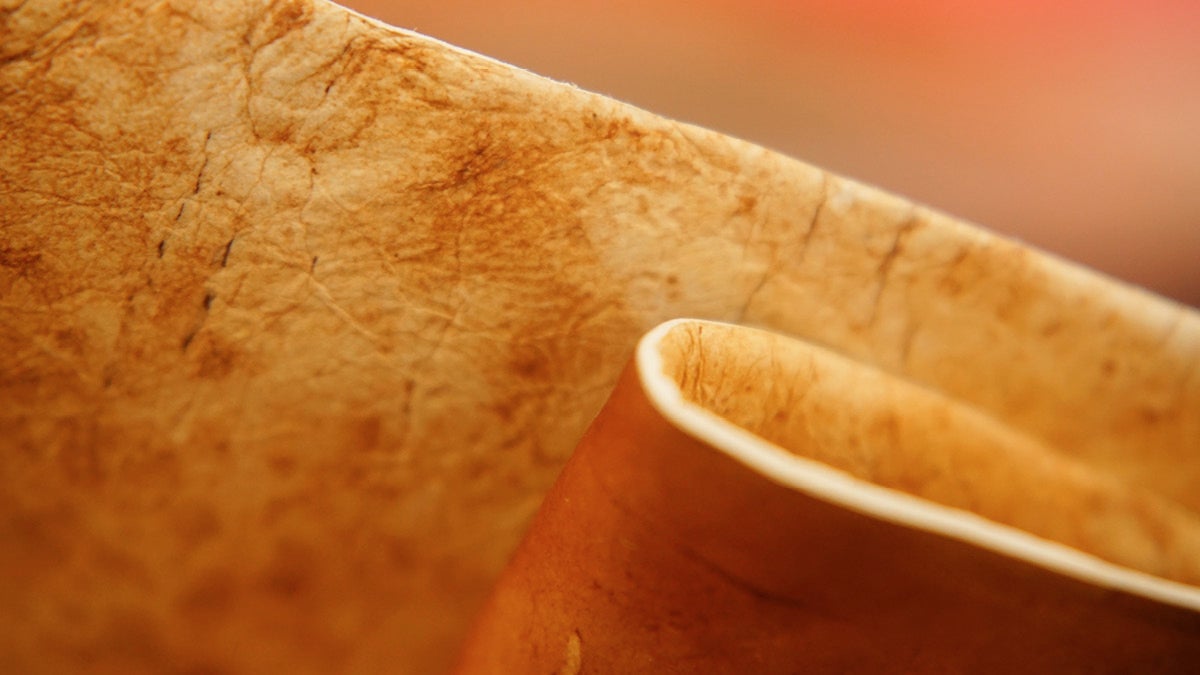
1. Fungal Leather
Demand for leather alternatives is growing as consumers increasingly question the ethical and environmental impact of wearing chemically treated animal hides. Yet synthetic substitutes for leather are no panacea as they’re derived from fossil fuels, require the use of hazardous chemicals in their production and are not biodegradable.
Fungal biomass, extracted from mycelium, offers a new and exciting way forward, according to a recent paper from the University of Vienna, Imperial College London and RMIT University in Australia, published in Nature Sustainability.
Producing fungal mycelium is typically low cost. It can be grown on sawdust or other forestry or agricultural waste, then treated to produce a leather-like textile, which can be as durable and flexible as leather, though is of course vegan and animal free. The growth of fungi is carbon neutral and, if it isn’t combined with other synthetic materials, biodegradable at end of life.
In the last five years, the use of mycelium as a sustainable textile has generated much academic and commercial interest. And companies in Italy, the United States and Indonesia have already produced prototypes. Mycotech from Indonesia have made handbags, trainers and wallets, while Bolt Threads in America collaborated on handbags and totes with Stella McCartney and Chester Wallace.
The low raw material costs and relatively simple production process also suggest fungal leather may be an attractive sustainable material for smaller businesses and designers to work with.
2. Pineapple ‘leather’
Since its launch in December 2014, Piñatex has gone from an innovative natural textile to a prolific leather alternative. Made from waste pineapple leaf fibres, it’s now used by more than 1,000 brands worldwide, including Paul Smith, Hugo Boss and H&M, for clothing and footwear, and by Hilton Hotels for soft furnishings.
Piñatex was invented by Dr Carmen Hijosa, who had the idea while consulting in the Philippines during the 1990s. There, she witnessed the environmental impact of mass leather production and chemical tanning, but also noticed the use of woven plant fibres in traditional garments and the abundance of discarded pineapple leaves left after the fruit was harvested.
Hijosa quit her job and did a PhD to develop a sustainable textile and scalable supply chain from that wastage. Of that decision, she says: “Design is not just about product. Design is about responsibility.”
After the pineapple harvest, the long fibres from the fruit’s leaves are extracted, then washed and dried by the sun, or in drying ovens during the rainy season, to produce a fluffy material. This is mixed with a corn-based polylactic acid to create rolls of non-woven mesh which are shipped to Spain and Italy for finishing.
Piñatex has proven to be a versatile natural fibre with good strength and flexibility. It’s available in a range of colours and finishes, including a waterproof version. On the downside, the product isn’t yet 100 per cent biodegradable as it’s made from two different materials, 80 per cent pineapple leaf fibre, 20 per cent polylactic acid.
3. Lab-grown ‘leather’
Dr Chetna Prajapati, lecturer in textiles within the creative arts at Loughborough University, was awarded a PhD for her work on biotechnology in textile design. One of the emerging sustainable fibres she’s most excited about is Zoa, a bio-based fabric made by US company Modern Meadow.
Zoa is created in a lab by using the DNA of yeast to make collagen, in a similar method to beer production. This collagen is then purified and shaped to create a leather-like material. “It’s a liquid,” says Prajapati. “So that allows you to be much more creative in the process, in terms of moulding it. And you’re not creating metres of fabric; it’s fabric without waste.
“Twenty years ago, people were saying this is the future; now we’re there. It’s just a case of scaling it up and trying to make it cost effective and accessible.”
What excites Prajapati the most is the change she believes emerging materials such as Zoa will have on the mindset of fashion designers, including her students.
“I think this is a great opportunity for them to re-evaluate what they’re doing, to stop and think about the impact of the fibres they’re using,” she says. “There is definitely an increase in awareness, and the ones who are really passionate will embed these principles into their projects and use it as opportunity to make conscious changes.”
4. Algae ‘cotton’
The Deep Green Biotech Hub at the University of Technology Sydney has the highest concentration of algae bio-scientists in the world. Their vision is to use algae, which absorbs carbon dioxide and produces more than 50 per cent of the oxygen we breathe, to replace fossil fuels.
Dr Mark Liu is a fashion designer collaborating with the hub to develop sustainable textiles made from micro-algae. “Algae is full of cellulose [cotton is 99 per cent cellulose] and it’s under our noses,” he says. “Micro-algae double in biomass in 24 hours, compared to cotton plants which take 100 days. We could be growing it in the sea instead of on arable land.”
Unlike algae which actually purifies water as it grows, cotton production is linked to water contamination and it requires huge amounts of water to grow.
The use of algae in the fashion industry is still in its infancy. It’s being used as a cotton substitute in a biodegradable t-shirt by Vollebak, combined with pulped eucalyptus and beech.
AlgiKnit has received seed funding to weave kelp fibres for use in footwear and fashion designer Charlotte McCurdy has made a water-resistant raincoat from algae.
“It’s still the very early stage,” says Liu, but he sees algae’s potential as vast. “You can have cotton replacements, but you can also replace polyester by growing algae as a lipid. Everyone is trying to find the algae that does the best job for the thing we’ve used before,” he says.
5. Orange ‘silk’
At the luxury end of the spectrum, Orange Fiber channels Italy’s high-fashion heritage and Sicily’s historic orange industry by spinning citrus waste into a silk-like sustainable textile. The business was founded in 2014 by Adriana Santanocito, who studied fashion design at AFOL Moda in Milan, and later patented a method for extracting cellulose from orange pulp and turning it into a silk-like yarn.
According to Orange Fiber, Italy produces 700,000 tonnes of citrus by-products a year, which proves difficult to dispose of. By upcycling these natural fibres, the company helps alleviate this waste burden, while catering to consumers who are increasingly looking at the environmental impact of the clothes they wear. The company also hopes its textile will spark new conversations around sustainability in the fashion industry.
Orange “silk” has a soft, lightweight feel and is biodegradable, though the fabric can also be blended with other materials. Salvatore Ferragamo was the first fashion house to use Orange Fiber fabrics throughout their collection in 2017 and in 2019 Orange Fiber produced a collection with H&M Conscious, the Swedish brand’s sustainable fashion line.
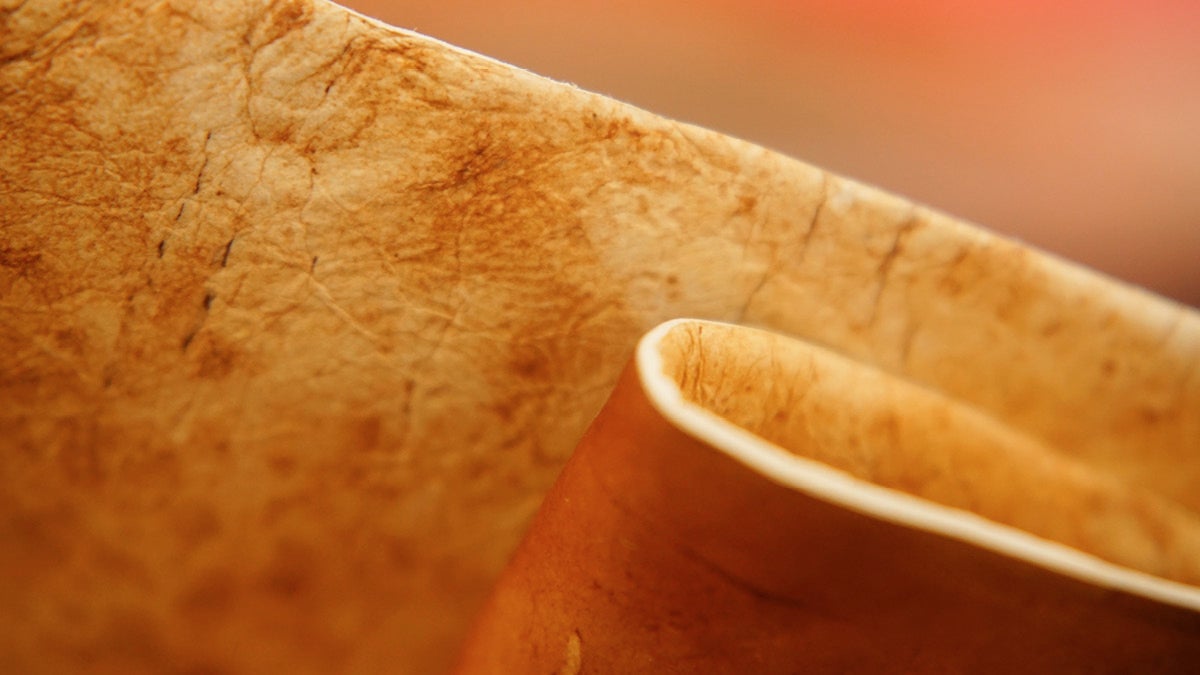
1. Fungal Leather
Demand for leather alternatives is growing as consumers increasingly question the ethical and environmental impact of wearing chemically treated animal hides. Yet synthetic substitutes for leather are no panacea as they’re derived from fossil fuels, require the use of hazardous chemicals in their production and are not biodegradable.
Fungal biomass, extracted from mycelium, offers a new and exciting way forward, according to a recent paper from the University of Vienna, Imperial College London and RMIT University in Australia, published in Nature Sustainability.