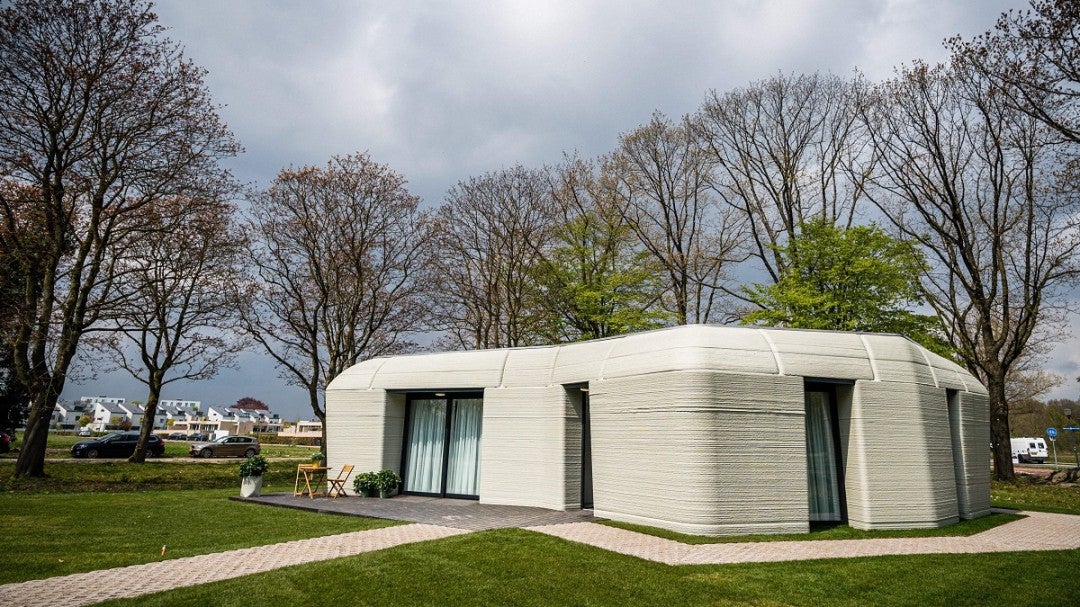
A 3D-printing business in the US says it can construct a home in half the time required to build a conventional equivalent – incurring only 10% of the labour cost and 10% of the waste. One of its rivals says it can print a house out for a shade over $10,000 (£7,100). It sounds rather too good to be true, doesn’t it?
One person who should know the answer is Henrik Lund-Nielsen. He’s the founder and general manager of Copenhagen-based firm Cobod, one of the world’s best-known house printers. His verdict? “The numbers you see are usually bullshit.”
First, the cost of the houses quoted in headlines is merely that of printing the concrete walls, he says. None of the other elements of the building – from windows to wiring – are priced in.
Second, there’s a lack of clarity about what’s actually printable. A pretty picture of a finished home suggests that the entire edifice came out of a nozzle. In fact, only its walls are printed. The rest of the building is made using more conventional methods.
“Try getting a young English kid to work in construction. They don’t want to, but they might want a job where they control a 3D robot with an iPad
And third, speeds are often overstated. Lund-Nielsen’s research suggests that one much-publicised printed house that took “one day to build” had been under construction for five months.
“The motivation is to gain the attention of investors,” he says. “There is a 3D project in China that attracted a lot of publicity. If the company behind it had told the truth, it would have got 10% of the coverage.”
The marketing tactics seem to be working, though. “How many 3D printed buildings in the world do you think there are?” Lund-Nielsen asks. “There are fewer than 50, but they are the probably the most celebrated buildings ever.”
Despite this, when you look through the hype there are still clear advantages to be gained by using 3D printing. Returning to the speed factor, the printer uses nozzles on robot arms to extrude a thick concrete – usually a mix of cement, sand and additives that accelerate the setting process – in layers. This method is genuinely fast. For instance, New York company SQ4D can make the walls of a 175m2 house in 48 hours of print time spread over eight days. This operation requires three people and the materials cost $6,000 – numbers that are hard to quibble with.
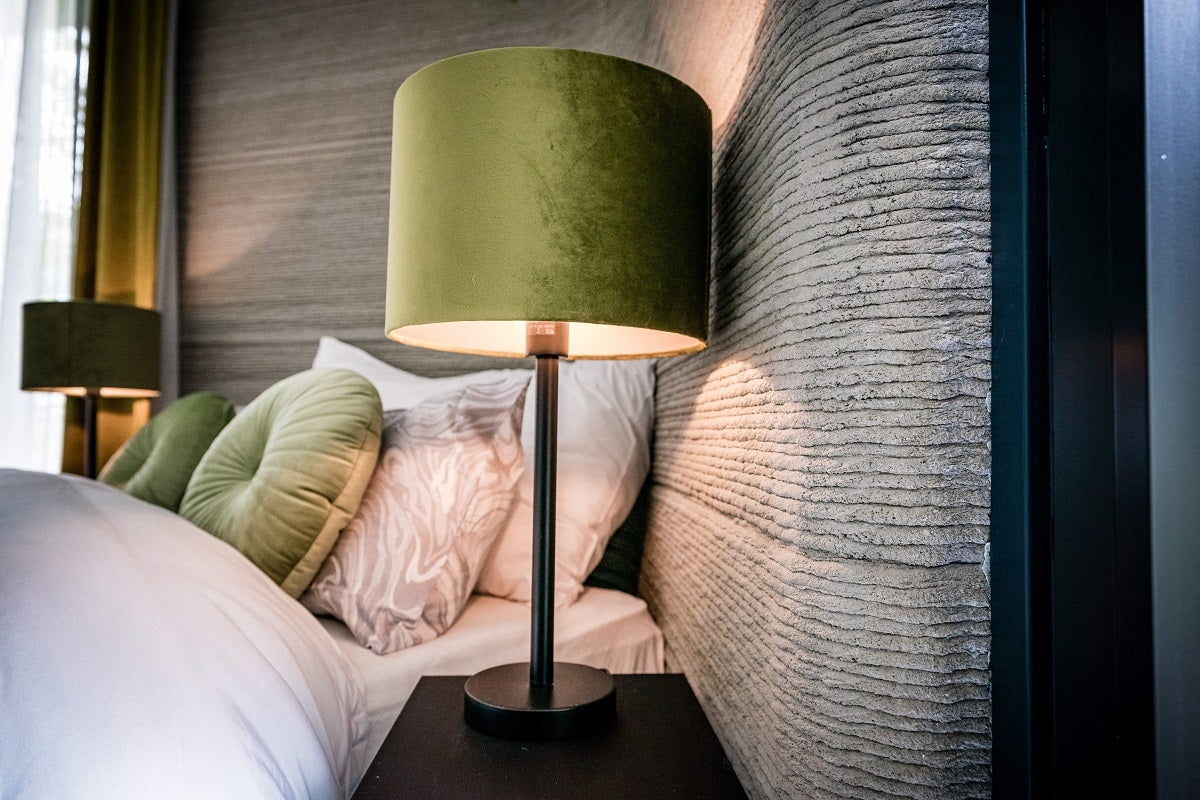
Then there’s design flexibility: the printers can produce any shape. Paolo Guglielmini is president of the manufacturing intelligence division at Hexagon, a developer of simulation software used by house printers such as Mighty Buildings. He says that printing offers “unique flexibility, because there’s a more direct link between digital design and production. You print ideas.”
Guglielmini goes on to extol the benefits of simulation: “After the design, material and process have been perfected at this stage, issues such as warpage, delamination and residual stress will all have been eliminated virtually when the home is printed, meaning there’s no need to waste time and money printing a four-tonne prototype that’s warped and not in spec.”
The range of building materials that can be used is expanding too, offering further flexibility. Light-gauge steel, for instance, can be printed on site or in a factory.
Jesus Jimenez is director at White Red Architects, which has been involved in a 93-unit housing project in Kent that’s using steel recycled from cars. “You build a skeleton from the parts, like a massive jigsaw,” he says, noting that the speed of the printing process slashes labour costs.
Every part can be printed bespoke – something that’s hard to do using traditional fabrication methods. This makes it possible to upgrade components of existing buildings with printed light-gauge steel. Jimenez says: “The tenants in one building to which we’re adding units don’t even need to move out.”
How many 3D printed buildings in the world do you think there are? There are fewer than 50, but they are the probably the most celebrated buildings ever
The more material in a build that can be printed, the more cost-efficient that project is likely to be. Buildings that don’t require much wiring, plumbing, tiling and other labour-intensive tasks are particularly suitable. It’s why Cobod has been looking into producing windmills and warehouses, says Lund-Nielsen, who believes that the labour costs associated with his sector of the industry will inevitably rise.
“Try getting a young English kid to work in construction,” he says. “They don’t want to, but they might want a job where they control a 3D robot with an iPad.”
Printing giant Ricoh thinks that the technology can add real value to humanitarian aid efforts. Richard Minifie, a senior engineer at the company, sees it as a disaster-relief solution in remote locations or a way to ease problems caused by overpopulation in the developing world, rather than a replacement for standard housing.
“There is clear potential for it in countries lacking skilled labour or where it’s hard to organise a workplace,” he says. “The first printed school in Madagascar is set to open its doors this year, for instance.”
In the future, robots will be able to perform tasks such as plastering and running cables. We may even see androids with superhuman strength working on site. Boston Dynamics has already built Atlas, a dextrous four-limbed robot with the ability to break through concrete panels.
So 3D house printing is here and, while the PR campaign surrounding it should be taken with more than a pinch of salt, it offers significant efficiency savings. For instance, California-based Mighty Buildings is offering to install a fully furnished one-bed house for $221,750 (£157,250). No hype – it’s ready to order today.
Even Lund-Nielsen – who estimates that “between 95% and 98% of the claims published by the industry are misleading” – believes that the technology is set to change the world. Coming from the arch-sceptic, that’s quite something.
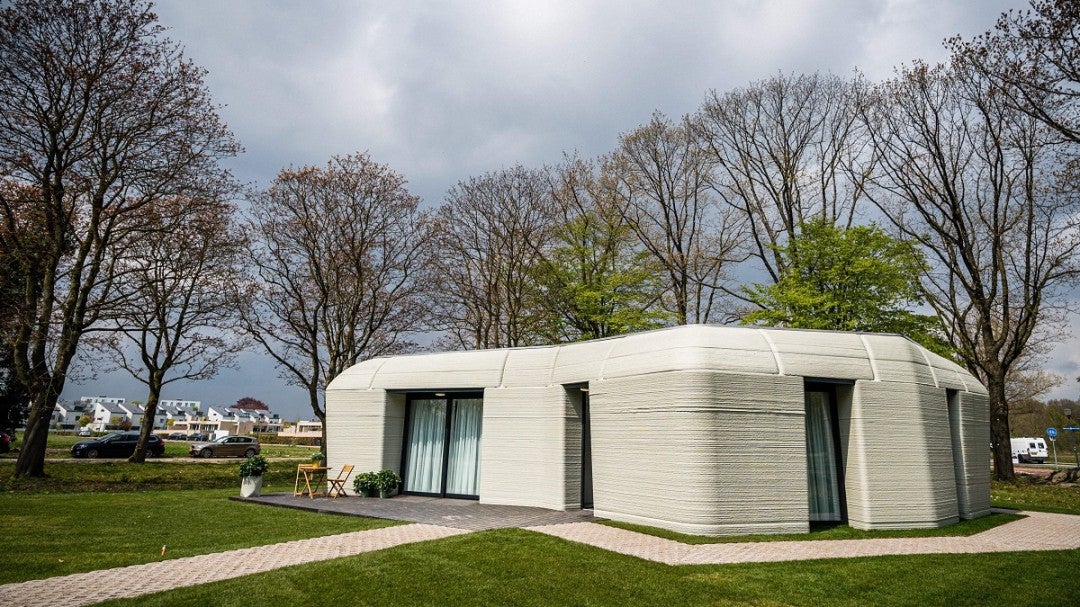
A 3D-printing business in the US says it can construct a home in half the time required to build a conventional equivalent – incurring only 10% of the labour cost and 10% of the waste. One of its rivals says it can print a house out for a shade over $10,000 (£7,100). It sounds rather too good to be true, doesn’t it?
One person who should know the answer is Henrik Lund-Nielsen. He’s the founder and general manager of Copenhagen-based firm Cobod, one of the world’s best-known house printers. His verdict? “The numbers you see are usually bullshit.”
First, the cost of the houses quoted in headlines is merely that of printing the concrete walls, he says. None of the other elements of the building – from windows to wiring – are priced in.