Few sectors epitomise the phrase “time is money” more than aviation.
Passengers may bemoan delays and disruptions but for the airline operator, with a plane on the tarmac grounded by mechanical failure, the frustration is even more acute. According to estimates based on a study from the Federal Aviation Administration, this inertia equates to a loss of $150 dollars a minute – and that’s being conservative.
With optimal reliability and uptime vital just to break even, squeezing every drop of efficiency from an aircraft’s assets has become the sector’s Holy Grail. Forecasts from aviation consultancy Cavok predict global sector spend on maintenance, repair and overhaul (MRO) will hit $100 billion by 2021, with smarter analysis of the data now flooding the aircraft playing a central role.
In turn, engine and airframe manufacturers are incorporating predictive models in their offerings to airlines, which not only help identify faults and component failures, but pre-empt issues before they escalate.
“Predictive technology is great at finding a needle in a haystack and helping engineers pinpoint the areas they need to focus on,” says Torsten Welte, global vice president for aerospace and defence at the enterprise software company SAP.
“With experienced aircraft engineers proving scarce and many now retiring, these solutions are set to become even more vital in gathering and utilising all this invaluable knowledge and information.”
Mr Welte traces the genesis of this traction to the power-by-the-hour approach to engine maintenance which Rolls-Royce pioneered in commercial aviation in the 1980s.
“When Rolls-Royce innovated the model with performance-based contracts that charge customers per flying hour of the engine, it became a case of ‘we must keep the engine running or we won’t make any money’,” he says.
“This changed the dynamics in the aviation industry between manufacturer and operator, and drove a different behaviour from the former that was now far more focused on getting the most out of their resources at all times.”
How airlines use data
The exponential rise in data usage has continued to fuel momentum. IBM figures reveal that an average aircraft generates between 500 to 1,000 gigabytes of data. Data analytic platforms such as SAP HANA tap into this business intelligence to monitor fuel speed, torque and pressure with internal predictive algorithms making recommendations in real time so parts can be sourced and engineers reassigned even while the plane is airborne.
And it doesn’t stop there. The technology is also able to tackle the information silos which have traditionally undermined the effective sharing of key intelligence across the aviation ecosystem.
Mr Weltes says: “In some countries, due to local ownership rights, performance data is owned by the pilot rather than the airline, which means they have to get permission to access it. Elsewhere, a manufacturer does not necessarily have access to maintenance data which is often owned by the airlines’ own maintenance systems, so it’s all very disjointed.
Predictive technology is great at finding a needle in a haystack and helping engineers pinpoint the areas they need to focus on
“Virtual data models get around this by allowing ‘read only’ access to the data irrespective of ownership, which most companies are more open to rather than transferring the data between different systems. This way the ownership is still with the airline or MRO, but the processing party can still access specific information at specific times.”
Another process undergoing significant transformation is the traditionally complex task of tail planning, in essence assigning the most appropriate aircraft to a flight route. For example, if an aircraft has an issue that adversely affects fuel burn, it will be allocated to the shortest flight.
Typically an airline would spend three to four hours working on a plan which can be subject to 150 changes daily. Until recently, the process had barely evolved from the handwritten schedules of the mid-1980s, with many airlines still transferring the information manually into spreadsheets comprising a dozen pages.
The current landscape
Dubai-based airline Emirates is one of the big names now automating the process, having adopted software vendor IFS Aviation and Defence’s predictive technology.
“Previously the plans were devised based on the judgment of someone with perhaps ten to twenty years’ experience, but our technology means we can tap into historical data that goes back forty years, all in a matter of minutes,” says IFS business development head Espen Olsen.
“Maintenance history, fuel consumption, climate, forecast – all these characteristics are put into the algorithm to calculate the best option, which means reduced risk, increased fuel efficiency, and improved fleet utilisation and maintenance planning.”
He believes the Middle East is driving this market. “They see an issue and do something about it without over-analysing the problem, and they are definitely ahead of Europe when it comes to using this technology. One manufacturer does something visionary and everyone follows,” says Mr Olsen.
More broadly, he is seeing a lot of interest from oil and gas companies inspired by the latest innovation in aerospace and defence. “There has been so much money in this market in the past, they didn’t have to consider how they could become more efficient,” says Mr Olsen. “Yet since the downturn, they are now far more focused on extending the life of equipment and how, as a service provider to the industry, they can commit to a ten-year contract on a fixed basis and still make money – increasingly predictive analytics has the answers.”
How airlines use data
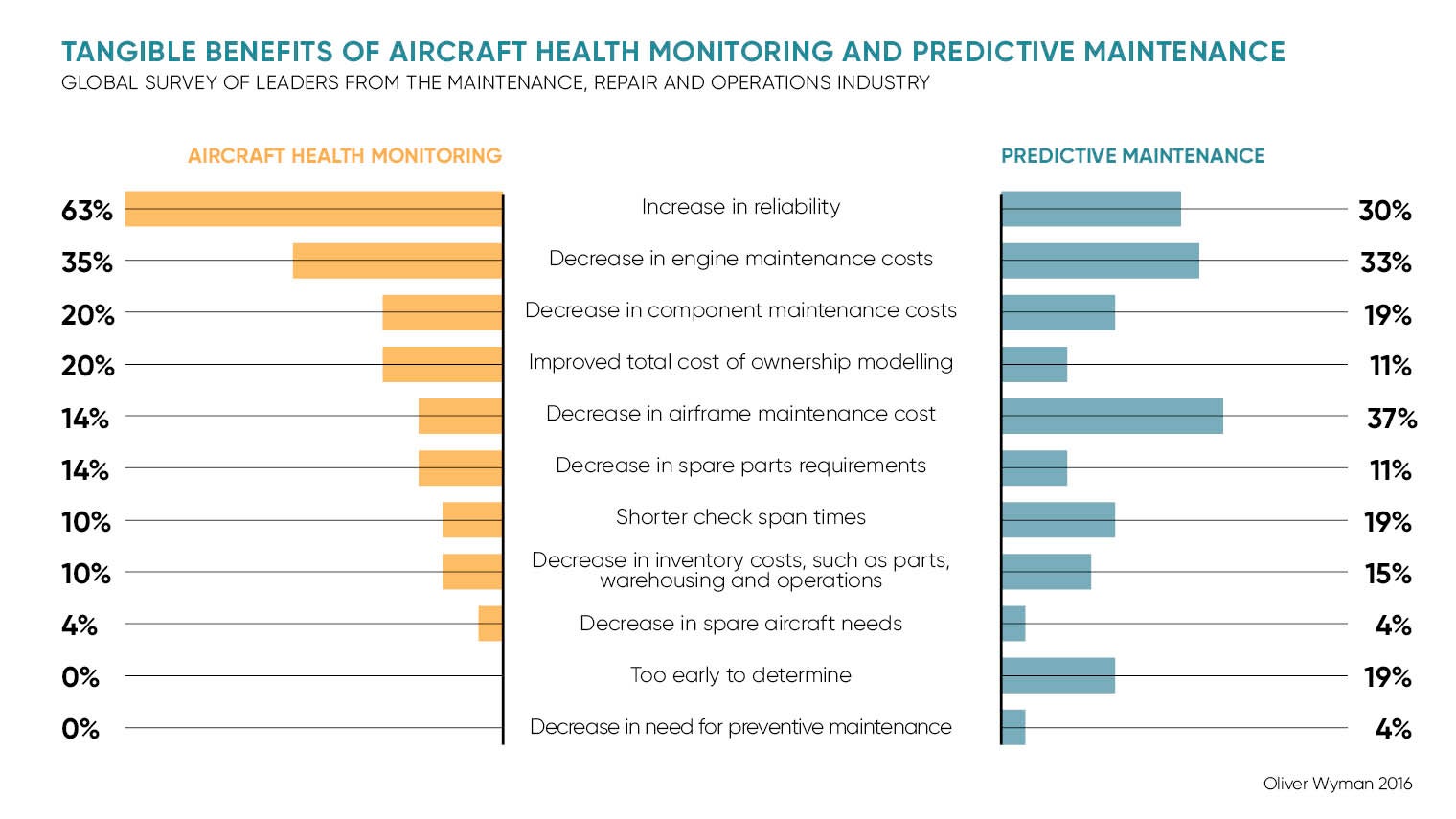