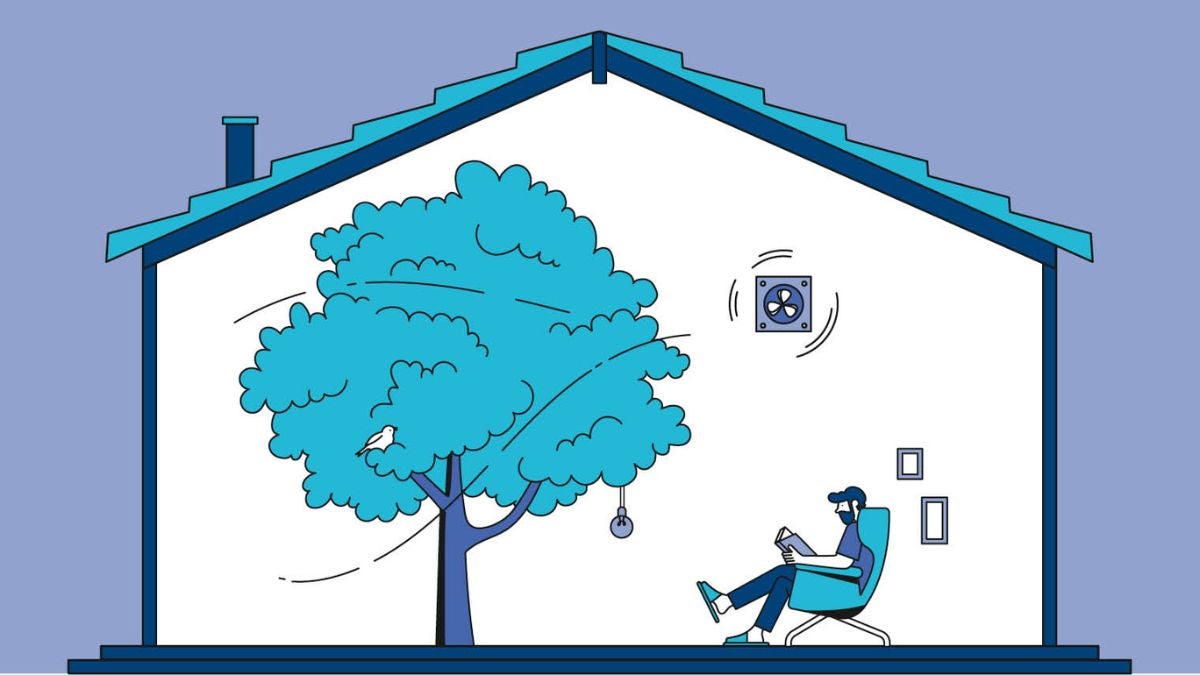
As we move towards making homes energy-efficient, looking back may not be intuitive. But Graeme Fox, who is head of technical at the Building Engineering Services Association, suggests that is exactly what we should do.
Fox points to homes that were built decades ago as having resonance in the design of today’s heating systems. The house he grew up in, for instance, had a central cupboard containing a warm air furnace, with ducts shooting off to different rooms: a central system that provided warm air from the building’s core.
After boilers and electric heating systems, technology has replicated something similar to that older design in mechanical ventilation heat recovery (MVHR). This more efficient system can provide around 3-3.5 kilowatts of heat for every kilowatt of electricity consumed. At the same time, it brings in new air from the outside and extracts stale, moist and polluted air, which improves indoor air quality. It significantly reduces energy used for heating as up to 91% of the heat from the extracted air can be retained and transferred to the incoming fresh air.
This is fundamental because buildings have ramped up energy-saving insulation, becoming more airtight and a lack of ventilation can have serious health implications. That’s why, on 15 June 2022, an update to Approved Document F of the Building Regulations came into effect, overhauling the UK’s rules on air quality and ventilation. Also updated was Approved Document L, which relates to the “conservation of fuel and power”.
Anybody interested in buildings – how they work, how you design them – should be looking at ways to make them more efficient
The two updates go hand in hand, as better insulation will be essential to reach net zero. To address its challenges, some businesses are investing in their infrastructure, whether that means MVHR, heat pumps or water recovery systems. And while the significant cost of such systems can’t be disregarded, adopting the long-term approach is a spur to boost efforts to achieve net zero.
The refresh may help the UK deliver net zero by 2050 but the Covid-19 pandemic has had more than a minor role in pushing for better indoor air quality.
It is also a step toward the Future Homes and Buildings Standard 2025. This new set of standards will ensure that homes built from 2025 will produce 75% to 80% less carbon emissions than under current regulations: the requirement is 30% this year. But some non-profits, such as the New Economics Foundation, say the benchmark has come too late after the scrapping of the zero-carbon homes standard in 2016, which would have forced net-zero carbon homes to be built by 2020.
Others believe the 2025 regulations should be set at or close to the Passive House standard (which aims to make heating and air conditioning systems obsolete) for fabric performance. A renewable heat requirement for new builds with a balanced retrofit target involving fabric improvements for existing buildings would also be welcome.
“Such a target, plus financial drivers such as an energy-saving stamp duty allowance, should also be announced now and implemented by 2025 so that the enormous task of improving all of the UK’s existing buildings can proceed in time to meet our 2050 net-zero targets,” says Jon Bootland, chief executive of the Passivhaus Trust.
Within industry, the new regulations are generally welcome, says Fox, as they provide needed clarity for the various applications of ventilation systems.
As well as MVHR, heat pumps are currently advocated with the government introducing a zero-rated fee. Fox says heat pumps have had a bad rep for high upfront costs but could be implemented more cheaply with split-level pumps.
“Outside of the sector, split-level pumps went under the radar. But they could be important in future home building,” he says.
Projects such as the Manchester Engineering Campus Development and the Devizes NHS Medical Centre are building smart, sustainable buildings that include energy efficiency and ventilation in their designs.
Benchmarks are there as guidance. You should never use them as the minimum
The Manchester development has technology-assisted window control to provide natural ventilation. It uses machine learning for automation and adapts according to occupant and energy needs. The Devizes medical centre is one of the UK’s first net-zero health facilities and uses heat pumps and solar panels for heat and electricity, saving around 25 tonnes of carbon a year. Its anticipated payback was 15 to 20 years, but the current energy crisis makes this likely to be sooner, according to a spokesperson for the project.
Retrofitting, however, is a difficult ask, explains Richard O’Brien, design director of housebuilder Northstone. This is because additional work is needed to adapt an older building, such as potentially adding more radiators. That’s why Northstone explored how every material used in a home could be made to work in its most sustainable way.
“Anybody interested in how buildings work, how you design them – should be looking at ways to make our buildings more efficient,” he says. “And it’s a continual process. Benchmarks are there as a guidance – never use them as the minimum.”
In a world where people are increasingly at risk of having to choose between warmth or food, working towards passive house principles could be powerful, says O’Brien.
“Businesses are competitive by nature, so step changes need to be incremental to avoid a massive impact on your business financially,” he reasons.
For now, much advocacy is needed to get all the different parties involved in the construction chain – contractors, specifiers, manufacturers – on the same design page, so that these relatively new standards and features work together holistically.
While the technology evolves, flexibility can be useful. That way, when the next set of targets makes sustainable design even more urgent, having some built-in adaptability could prevent retrofitting from becoming the conundrum it is today.
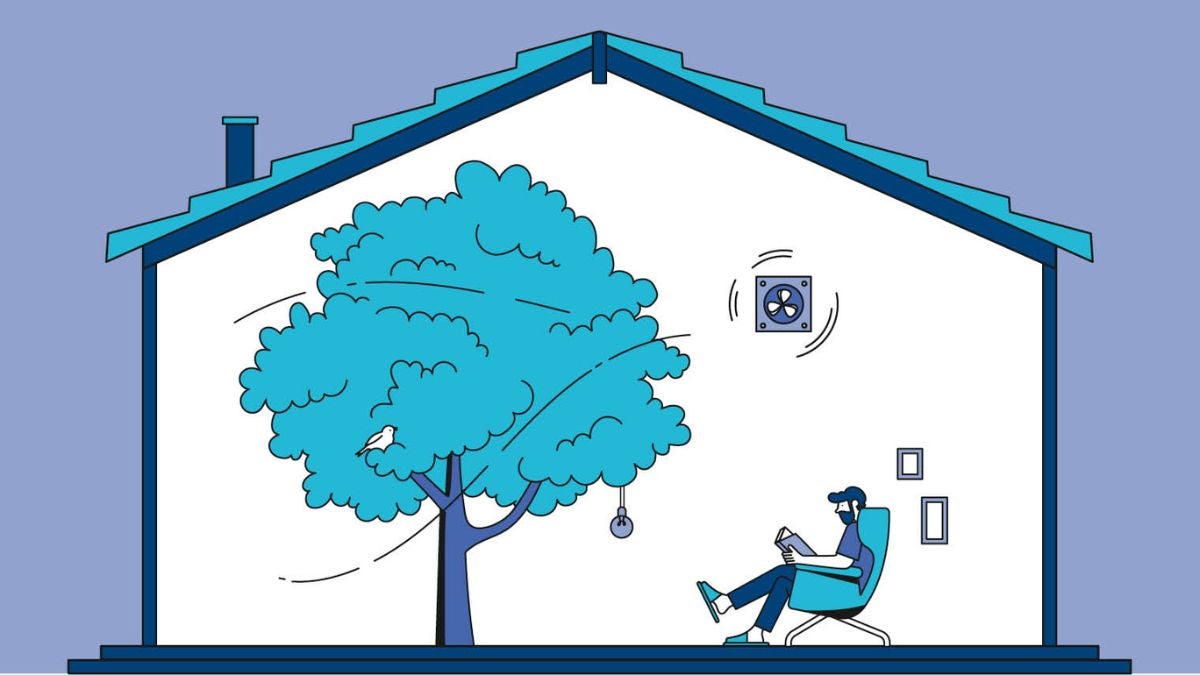
As we move towards making homes energy-efficient, looking back may not be intuitive. But Graeme Fox, who is head of technical at the Building Engineering Services Association, suggests that is exactly what we should do.
Fox points to homes that were built decades ago as having resonance in the design of today’s heating systems. The house he grew up in, for instance, had a central cupboard containing a warm air furnace, with ducts shooting off to different rooms: a central system that provided warm air from the building’s core.
After boilers and electric heating systems, technology has replicated something similar to that older design in mechanical ventilation heat recovery (MVHR). This more efficient system can provide around 3-3.5 kilowatts of heat for every kilowatt of electricity consumed. At the same time, it brings in new air from the outside and extracts stale, moist and polluted air, which improves indoor air quality. It significantly reduces energy used for heating as up to 91% of the heat from the extracted air can be retained and transferred to the incoming fresh air.