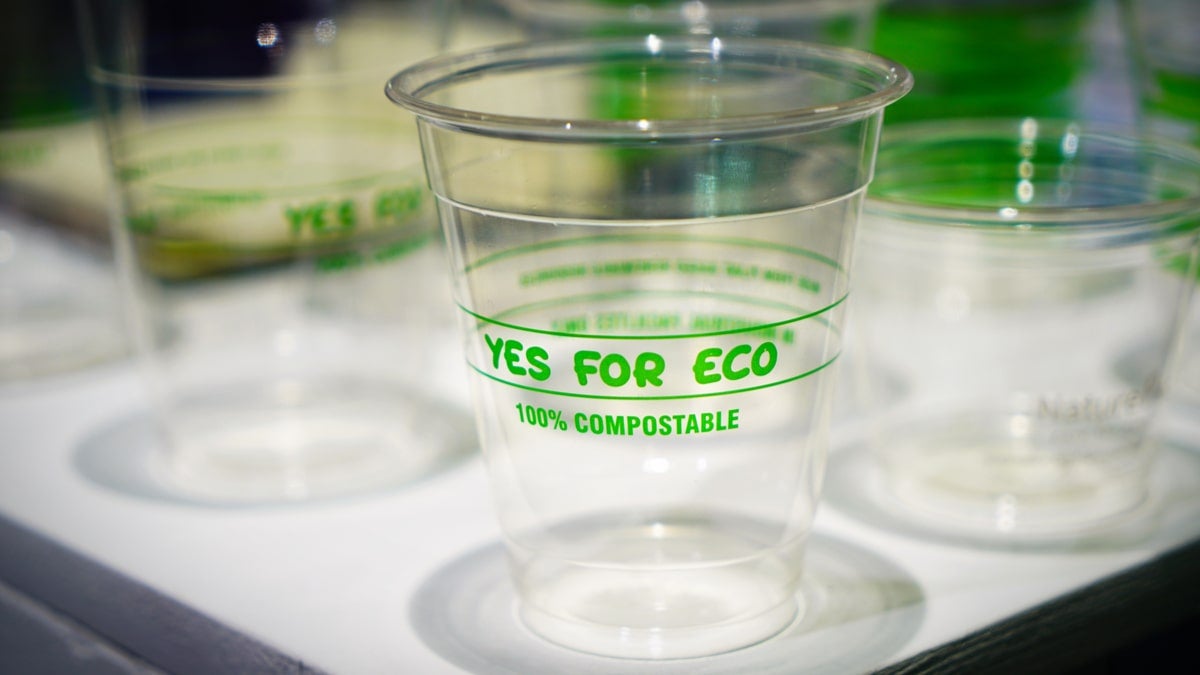
In the five minutes it will take you to read this article, 3,500 tonnes of plastic will have been produced around the globe. If that stat isn’t sufficiently alarming, consider the fact that barely 9% of the world’s annual output of 368 million tonnes is recycled, either because the process isn’t deemed economically viable, or because of a lack of consumer awareness.
Inventors and start-ups have been working hard in recent years to develop greener solutions. These have included everything from seaweed-based straws to toothbrushes made using bamboo. The problem is that many of these innovations are niche and can’t yet be scaled up commercially.
Most bioplastics – polymers derived from plant-based sources – that are touted as viable alternatives to petroleum-based plastics are usually produced from the sugars extracted from certain cash crops. The most popular of these polymers is polylactic acid (PLA). It’s being used increasingly in items such as disposable cups, cutlery and salad containers.
Another is polyethylene furanoate (PEF). There are high hopes that this can become the standard for bioplastic use in the food and drink industry. Companies such as Dutch firm Avantium are using plant-to-plastic technology to convert fructose syrup from wheat, corn and beet into the components of PEF, for instance.
This has attracted the attention of Carlsberg, Coca-Cola and Danone, among others. The hope is that a number of popular beverages could be coming in paper bottles lined with PEF in only two years’ time.
Competing with the food industry
As bioplastics gain popularity, questions are being raised as to how sustainable these materials really are. One issue is whether the sector’s future growth will affect the food industry if both have to compete for feedstock.
This is an unlikely scenario, according to Paul Mines, CEO of Biome Bioplastics. He observes that total area used for bioplastics production in 2020 came to less than 0.015% of the world’s agricultural land. This will rise to 0.02% by 2025 if the industry’s production capacity increases by the expected 25% from its current level to 2.8 million tonnes.
Avantium’s CEO, Tom van Aken, agrees. “Creating bioplastics from plant-based feedstock can be managed in such a sustainable way that it doesn’t have to be in competition with food production,” he says. “Increased demand for non-food applications could support a healthier agriculture sector through investments in sustainable land use. There is tremendous potential to use waste from sustainable forestry management, for instance.”
Van Aken predicts that the chemical and materials industries will work closely with farmers to build new supply chains, ensuring that no part of their crop is wasted. Bioplastics could be made using feedstock sugar residue from agricultural production, for instance. To this end, Avantium already has a partnership in the Netherlands with Cosun Beet Company, which produces sugar products for the retail and food service industries.
Not all bioplastics are created equal
Although the term ‘bioplastics’ has an eco-friendly ring to it, not all of these materials are actually biodegradable or compostable. Much depends on the polymers used and, even then, the conditions need to be right for decomposition – most bioplastics need to be subjected to high temperatures. The European standard EN 13432 for industrial composting requires 90% of a given material to biodegrade within 12 weeks. Complete disintegration must occur within six months.
We have to be aware that any material produced, even plant-based, can have an impact on the environment if the loop isn’t closed
In cases where industrial composting isn’t possible, the best option is recycling. Even then, the various bioplastics would need to be handled in separate streams, while some countries don’t yet have facilities that can break down polymers such as PLA. If not dealt with properly, bioplastics can end up in landfill anyway, defeating their purpose.
“We have to be aware that any material produced, even plant-based, can have an impact on the environment if the loop isn’t closed,” says Laetitia Van de Walle, CEO of Lamazuna, a French supplier of zero-waste natural cosmetics. Among its products is the Oriculi, an ear swab made using a bioplastic derived from castor oil.
“Controlling the lifecycle of any product is incredibly important,” she adds, noting that bioplastic recycling channels need to improve markedly if the materials are to become commercially successful.
Adjusting our thinking
Despite all best intentions to close the loop, bioplastics will find their way into the natural environment and become long-term pollutants, just like their petroleum-based counterparts.
It is not enough to simply develop solutions that fit the circular economy. There needs to be broader change, according to Mines. He hopes to see a transition to a bioeconomy, based on chemicals, fuels and products, where the processes of creating energy and materials go hand in hand.
“The petroleum-based plastics industry has spent a lot of time optimising its supply chains,” Mines says. “Replacing its products with bioplastics will require an adjustment in thinking. Continued consumer pressure, policy changes and brands deciding to alter practices will drive the transition.”
Until then, the bioplastics sector must continue innovating to ensure that the loop is closed. It must also create awareness about its products’ game-changing potential, while acknowledging that they’re not the panacea for the world’s plastic problems – not yet, anyway.
Van de Walle sums it up best. “We believe in the future of bioplastics,” she says. “But we know they’re still far from perfect.”
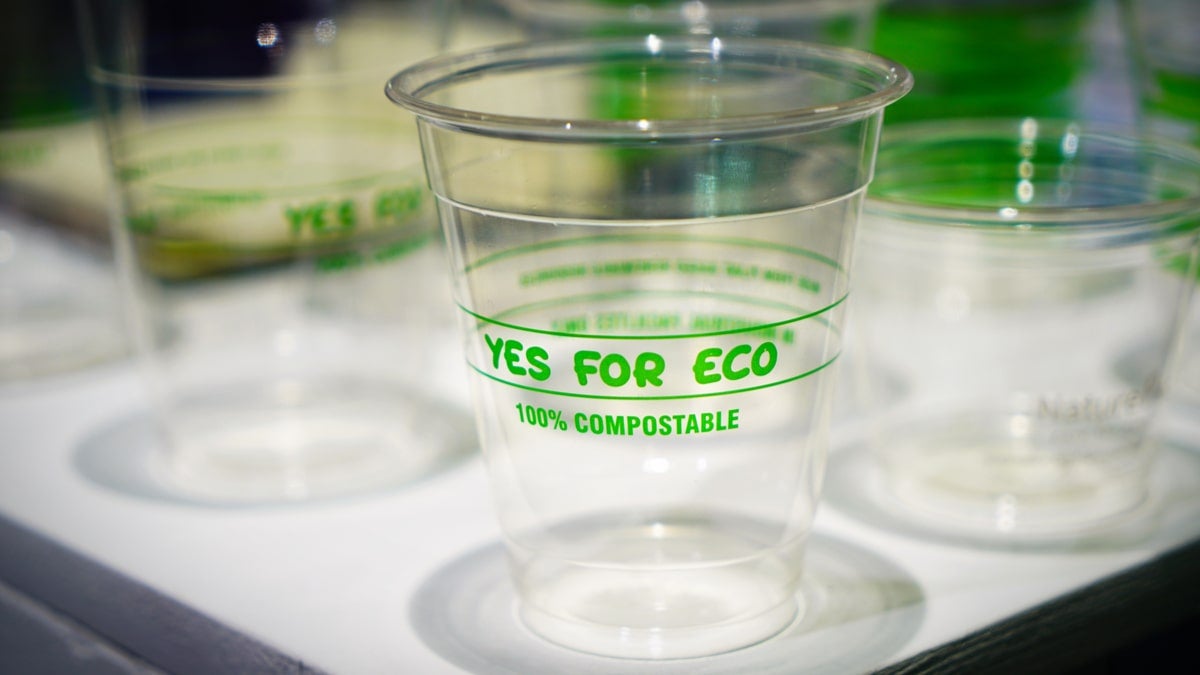
In the five minutes it will take you to read this article, 3,500 tonnes of plastic will have been produced around the globe. If that stat isn’t sufficiently alarming, consider the fact that barely 9% of the world’s annual output of 368 million tonnes is recycled, either because the process isn’t deemed economically viable, or because of a lack of consumer awareness.
Inventors and start-ups have been working hard in recent years to develop greener solutions. These have included everything from seaweed-based straws to toothbrushes made using bamboo. The problem is that many of these innovations are niche and can’t yet be scaled up commercially.
Most bioplastics – polymers derived from plant-based sources – that are touted as viable alternatives to petroleum-based plastics are usually produced from the sugars extracted from certain cash crops. The most popular of these polymers is polylactic acid (PLA). It’s being used increasingly in items such as disposable cups, cutlery and salad containers.