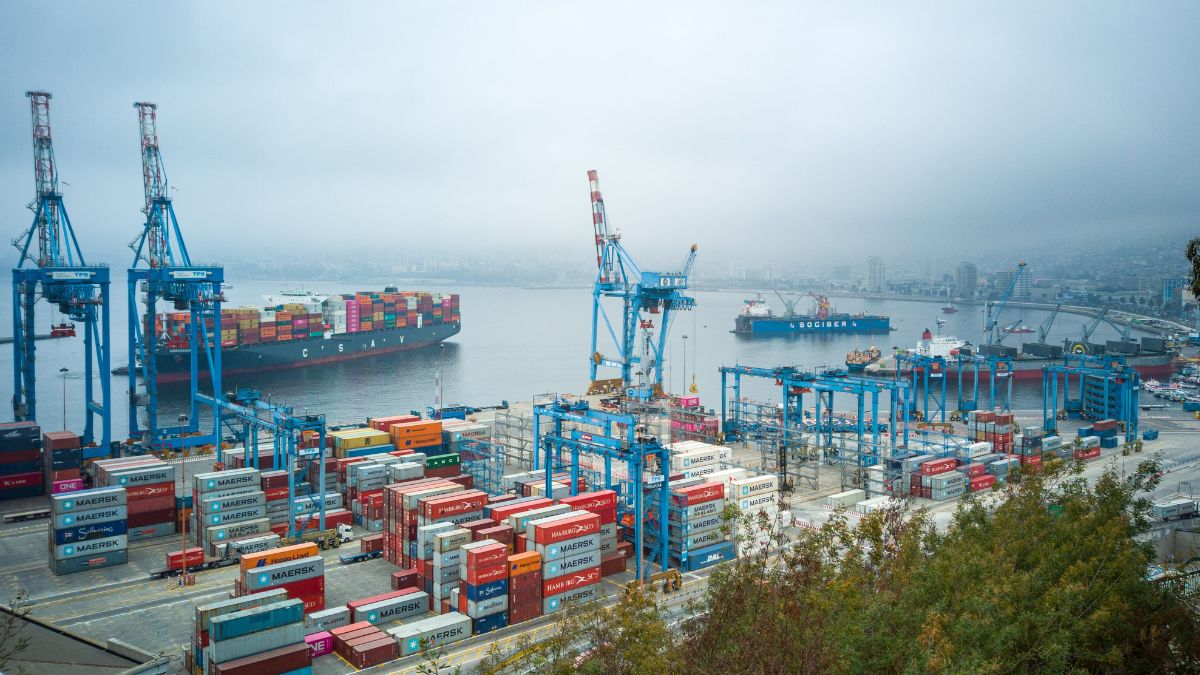
The race to achieve net-zero carbon emissions targets is intensifying as concerns deepen over global warming. Despite wind and solar plants easing reliance on fossil fuels, renewable energy companies are aware that they too have emissions challenges to resolve because of their supply chains.
Take wind power. The turbine blades contain petrochemical-based resins, while transporting them by sea or air produces carbon emissions, as does the extraction and production of the concrete, steel and other metals used in their manufacture. In the solar industry, polysilicon is a key material in solar panels and 75% of global capacity resides in China. But there have been worrying reports of forced labour and coal power used in its production in China.
Consequently, there is growing pressure on renewable energy players to do more to make their supply chains more sustainable. At the end of COP26 in Glasgow, summit president Alok Sharma urged the renewable industry to “drive action across your supply chains, encourage your suppliers to commit to net zero and work with them to reduce emissions”.
It is no longer enough to generate green power
In March, the Clean Energy Buyers Institute launched the Decarbonizing Industrial Supply Chain Energy initiative, which aims to increase awareness and develop tools to decarbonise the solar photovoltaic supply chain. It wants energy customers and developers to partner and work to enhance clean energy procurement and decarbonise building materials. Renewable energy trade association RenewableUK has been encouraging its members for some time to think sustainably. In 2020, it launched the Member Values Charter which committed signatories to reducing emissions from operations and products.
“When you are a renewable energy developer you are, rightly, held up to even greater scrutiny than in any other sector. It is no longer enough to generate green power,” says Robert Norris, head of communications at RenewableUK. “You need to look at every part of your supply chain to make sure it is as green as possible. That includes where the raw materials are sourced and moved.”
And renewable firms are also responding. Siemens Gamesa makes wind turbines and intends to make its wind turbines fully recyclable by 2040. The towers and electrical components made of copper can be used again but the blades of wind turbines are trickier as they are made of composite materials. They are usually sent to landfill or incinerated after reaching the end of their working lives. Now, though, by using new technology to separate the composite materials the blades can be recycled into new applications. In the Danish port city of Aalborg, home to one of Siemens’ manufacturing plants, authorities have repurposed discarded wind turbine blades as bike shelters.
Vestas Wind Systems, which also manufactures turbines, isn’t being left behind in the slipstream. It is developing recyclable blades as part of its sustainability strategy. It is focused on creating a value chain that generates no waste materials and reducing the CO2 emissions from its supply chain by 45% per MW/hour generated, by 2030. As part of this plan, Vestas is working with 27 key suppliers by asking them to commit to using 100% renewable electricity, set carbon emissions reduction targets and measure production waste.
Renewable energy developer Vattenfall has also vowed to reduce its supply chain emissions from goods and services – by half, by 2030. Its main emissions drivers are the extraction and production of raw materials and transportation. Part of its attempt to tackle the problem, it says, is making climate-smart design choices. This includes developing concrete with a lower share of cement for a new hydropower dam in Sweden. During the construction of an onshore wind farm in the Netherlands, it has also introduced the environmental cost indicator in its procurement process. This assessment of the life cycle involves asking suppliers how they would reduce their ECI value using their design, machinery, transport, work, and material improvements.
Those with a high expected reduction gained an advantage in the supplier selection process, leading to reduced emissions of greenhouse gases on the project compared to normal builds.
“We have had a focus on reducing emissions for some time, but we wanted to create a firm target for suppliers,” explains Vattenfall’s head of sustainability Annika Ramsköld. “But, the biggest carbon footprint is rarely with our direct suppliers. It is usually much further down the supply chain with steel, cement and aluminium, which we don’t buy directly.”
The embryonic nature of parts of the sector can be an issue in finding green and ethical suppliers. Ian Johnston, chief executive of EV group Osprey Charging Network, says it has had a sustainable supplier framework in play since 2020. “But the challenge for a business like ours in a relatively nascent market like EV charging, is that we do not yet have a wide range of hardware suppliers to select from,” he says. “The ease of use of the hardware we install is a critical factor in driver satisfaction but we are fortunate that sustainability is such an important factor across our industry that our hardware partners are also making strong strides forward.”
The biggest carbon footprint is rarely with our direct suppliers. It is usually much further down the supply chain
Meanwhile, supply chain experts Achilles is doing its best to make the sector more visible for other new entrants, such as legacy oil and gas firms, through its Green Energy Network. It provides global prequalification services and ESG scoring of potential renewable energy suppliers to help developers to build new supply chains. “There is massive opportunity now as the industry ramps up, but it is creating growing pains. A lot of swift supply chain building is needed,” says chief product officer Katie Tamblin. “When there are so many new suppliers entering the market, it is difficult to ensure that the supply chain is ethical and sustainable. You need full visibility of the carbon footprint across multiple tiers of the supply chain – as well as governance and issues such as labour rights. There are a lot of risks.” One potential answer – driven by the Russia-Ukraine war and the need for energy security – is the localisation of supply.
Vattenfall is aiming to reduce its exposure to steel and is part of the Hydrogen Breakthrough Ironmaking Technology project, alongside Swedish steel manufacturer SSAB and mining group LKAB. The purpose of HYBRIT is to create fossil-free steel, using hydrogen. The US has barred imports of Chinese polysilicon and, as part of its ramp-up of offshore wind production, has asked bidders to include plans to support port development and the supply chain. In the UK, developers of projects that have a capacity above 300MW must include supply chain plans in their bids. The government has also funded a new turbine tower factory in the Port of Nigg in Scotland to increase local production.
“The government is keen on creating these offshore wind hubs,” says Norris. “It leads to a lower carbon footprint than importing materials or getting them from elsewhere in the UK. It is an interesting blueprint for the future and another example of our industry walking the walk on sustainability.”
Initiatives like these will surely help to halt the progress of global warming. There is always, of course, room for further innovative thinking in the bid to decarbonise industrial supply chains.
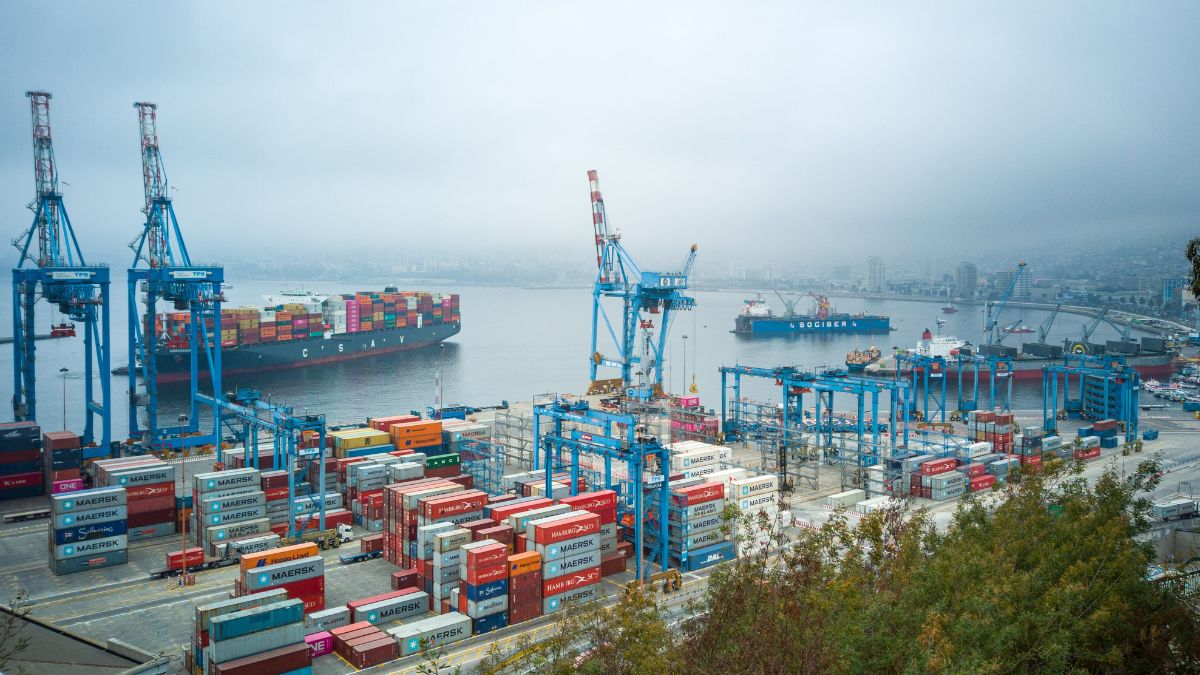
The race to achieve net-zero carbon emissions targets is intensifying as concerns deepen over global warming. Despite wind and solar plants easing reliance on fossil fuels, renewable energy companies are aware that they too have emissions challenges to resolve because of their supply chains.
Take wind power. The turbine blades contain petrochemical-based resins, while transporting them by sea or air produces carbon emissions, as does the extraction and production of the concrete, steel and other metals used in their manufacture. In the solar industry, polysilicon is a key material in solar panels and 75% of global capacity resides in China. But there have been worrying reports of forced labour and coal power used in its production in China.
Consequently, there is growing pressure on renewable energy players to do more to make their supply chains more sustainable. At the end of COP26 in Glasgow, summit president Alok Sharma urged the renewable industry to “drive action across your supply chains, encourage your suppliers to commit to net zero and work with them to reduce emissions”.