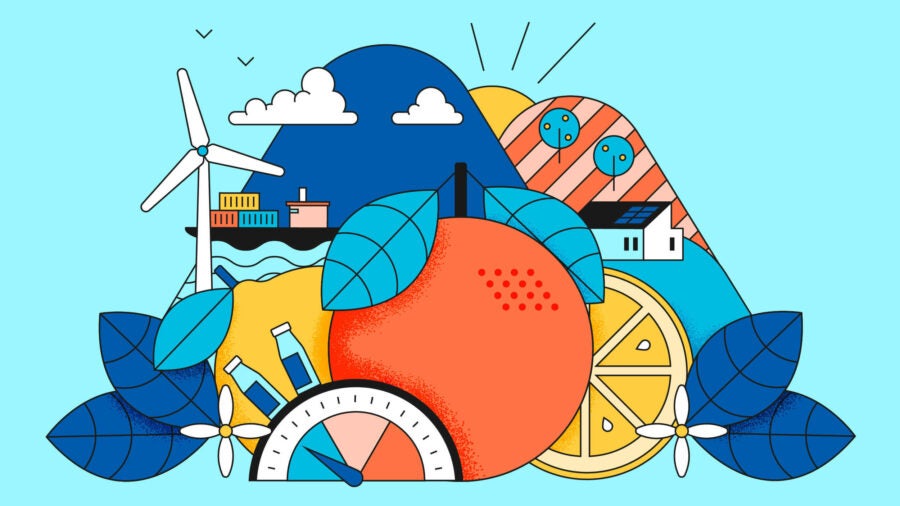
Rotterdam Port is an unlikely spot for a landmark green investment. The largest seaport in Europe stretches for miles in a drab maze of rusted drums, slag heaps and stacks of shipping containers. But on the far side of a scrubby field packed with seagulls pops a familiar halo logo.
It sits atop Innocent Drinks’ new €225m (£198m) factory, dubbed the Blender. Despite its unassuming setting, the factory is packed with technology aimed at making it one of the world’s first carbon-neutral, all-electric drinks factories.
Innocent is a household name in the UK for its colourful, healthy smoothies and juices and quirky branding (its London HQ? Fruit Towers. CEO? Chief squeezer). But the company might be almost as well known for its ethos.
Ever since it was founded in 1996 by a group of university friends, it has set out its case for “doing business in the right way”. A B-Corp from 2018, Innocent gives 10% of its profits to charity and has set a science-based target of being carbon neutral by 2025 and net zero by 2040.
Why bring manufacturing in-house?
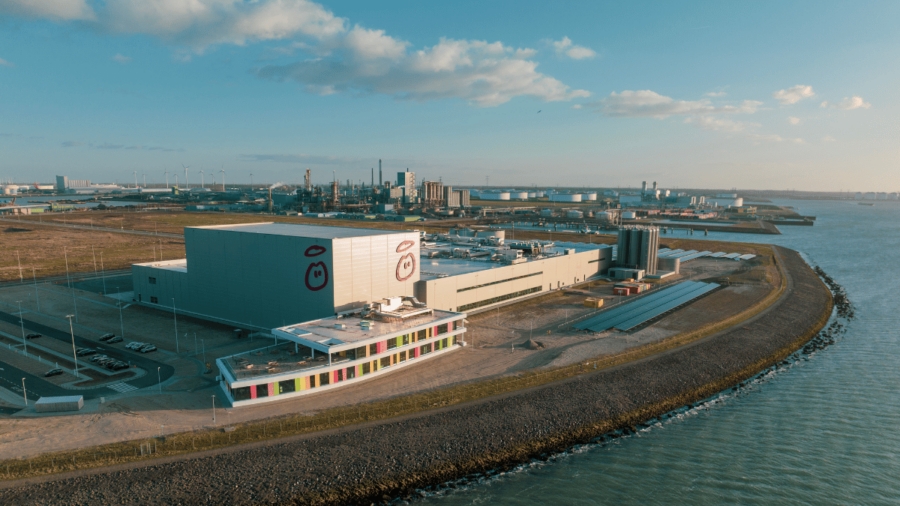
One roadblock in achieving those environmental targets was the fact that Innocent outsourced all of its processing and bottling to a patchwork of suppliers across the UK and Europe.
“24 years ago, smoothies weren’t really a thing,” says Emily Wakeford, supply chain lead at Innocent, as ships glide past the Blender office’s windows. “So our historical supply chain was really segregated. We had a place doing cold ingredients, a place doing blending, many other places doing bottling: every step was separate.”
When Innocent first started talking about bringing it all in-house, the aim was to save money and cut down on road miles from transport between facilities. But the company soon realised there was scope to do more.
“As the team started to look at it, we asked, if we’re going to build [a factory] – and this goes right back to the DNA of Innocent – how do we do it in the right way?” says Karina O’Gorman, European head of ‘force for good’. That meant designing a new factory from scratch with sustainability considered at every stage.
The ingredients of a sustainable factory
On a stroll around the gleaming, strawberry-scented factory – the smell changes each day depending on what recipe is being mixed up – the Blender’s site manager shows Raconteur how it all works.
First up, the factory is designed to run entirely on renewable power. Thousands of solar panels supply about 7% of the site’s electricity, with the rest coming from a renewable tariff on the grid. On-site wind turbines, which currently going through the planning process, will eventually take over.
Inside, everything is electric, from the machines that fill and seal bottles to fully-automated robots that pick and pour drums of fruits and purees.
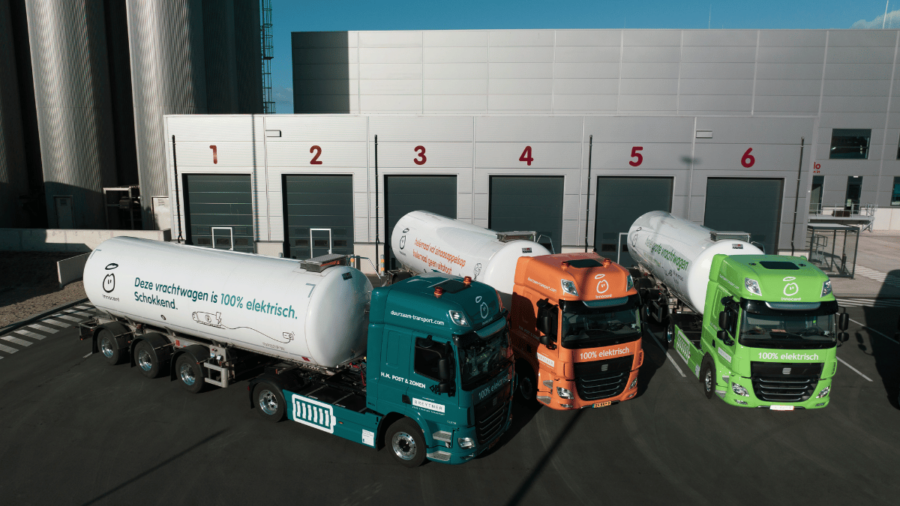
Instead of traditional gas-fired heating and cooling systems, the Blender employs a heat pump which works much like a domestic version. Waste heat generated by refrigeration is captured and used to pasteurise drinks.
The network of pipes connecting the blending, mixing and bottling equipment is kept spotless with an ‘air tornado’ system that shoots compressed air to remove grime. This reduces water use by 50% compared to conventional systems.
One of the biggest innovations is a “world-first” fleet of 50-tonne all-electric trucks. Something like a cartoon version of an oil tanker in appearance, they ferry orange juice to the Blender from a storage depot 40 minutes across the port, where it arrives on a ship from Brazil. Orange juice is Innocent’s main ingredient, and the bottled version is its first product to be certified as carbon neutral.
Even the factory’s incongruous location was chosen with sustainability in mind. Rotterdam port is where much of the fruit used in Innocent’s drinks arrives from South America and India – meaning 20% of truck miles could be slashed right away.
The port’s leaders have been “incredibly supportive of us coming in and trying to do manufacturing in a different way,” says O’Gorman. “The whole port was already trying to move towards renewable energy: there are quite a few wind turbines around.”
Indeed, several can be seen through the Blender office’s huge windows that overlook the North Sea: just one of the touches, along with bright colours, natural materials and greenery, that make it “a great place to work and a factory for people,” O’Gorman says.
“We’re the first ever manufacturing facility that’s aligned to the WELL framework [for buildings that promote wellbeing]. It looks at the health, wellbeing, air quality and environment.”
One thing the team couldn’t achieve was retrofitting an existing facility to avoid construction emissions. It would have been “near-on impossible” due to the scale needed, says O’Gorman, adding “and we didn’t own any factories in the first place.” However, reclaimed concrete and recycled materials have been employed where possible.
A blueprint for sustainable design
All that effort paid off when the factory was certified by BREAM NL, a sustainable building standard, as ‘outstanding’, the highest possible grade. It was particularly rewarding because the team did not have a template for what they wanted to achieve, O’Gorman says.
“There were times when we weren’t sure we were going to get where we wanted to get… it became a bit of an academic challenge for our partners and for us to look at the technological solutions.”
Close collaboration with those partners, including heat pump specialists GEA and the Dutch government, was essential to get the Blender over the line.
We want this to be a blueprint and inspire that change for everyone
“Suppliers found it really unusual to be asked if this was going to be your own pet project, how would you do it?” says Wakeford. “That’s often where people are waiting to be given the freedom to go, ‘I’d do it like this’. Often, that’s where the golden nuggets came from.”
Added to that was the hurdle of becoming a manufacturing company. For the first time, the team had to truly understand all the work previously done by suppliers, as well as upskill existing staff and hire for brand-new roles and teams.
They hope that the next company to follow in their footsteps will not find it as hard, however. Innocent is producing a white paper that will include “warts-and-all learnings and failures”, O’Gorman says. “We want this to be a blueprint and inspire that change for everyone. So if competitors asked to come in, we have no issue with that – we’ve had loads of other businesses already come in to have a look.”
In fact, if all companies manufactured in the same way, Innocent reckons it would cut 30% of their overall energy consumption.
Innocent and sustainability
Although the factory is a big step for Innocent’s green efforts, the company’s sustainability credentials have come under fire in recent years. It became a poster child for greenwashing when the UK’s Advertising Standards Authority (ASA) ruled that a 2021 TV advert about “fixing up the planet” was misleading to consumers.
Its ownership is also controversial. Innocent was bought out by Coca-Cola, one of the world’s biggest plastic polluters, in 2013. For some, it’s an arrangement fundamentally incompatible with claims to ethical business.
Innocent’s team are keen to stress that the relationship between the companies is largely arms-length. However, Coca-Cola did stump up the cash needed to build the Blender. Coke representatives have visited the factory more than once and Innocent hopes they will be able to feed learnings from it into their own manufacturing processes.
“This is their investment in us,” O’Gorman says. “Almost a quarter of a billion – it’s not cheap – because they want to see how you could build sustainable manufacturing… We get to keep our independence and be our fun, quirky selves, but we’ve got the support of Coke to actually make that happen.”
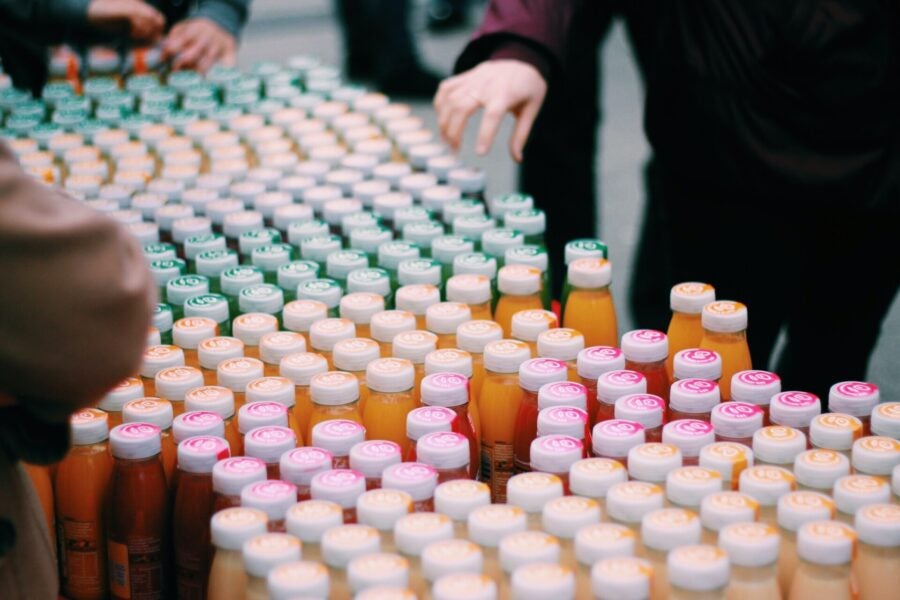
Cutting down on plastic will be another hurdle. Activist group Plastics Rebellion has claimed that Innocent pumps out 32,000 bottles an hour.
It’s been a goal for years, O’Gorman says. At present, 50% of the plastic used in their bottles is recycled, while some bottles contain an extra 15% of plant-based material. Innocent is campaigning for government deposit return schemes for bottles across Europe and has removed 2,500 tonnes of plastic from its annual packaging total by making their bottles thinner and lighter.
Then there’s the question of how much the new factory will reduce the company’s overall emissions. Just 5% of its emissions are down to bottling and processing, with the vast majority stemming from ingredient and packaging production and transport (although Innocent has several green programmes underway in those areas, too).
It means a portion of Innocent’s journey to carbon neutrality rests on buying carbon offsets, a contentious method. A Guardian investigation recently found 90% of rainforest offsets offered by one supplier, Verra, did not remove any carbon.
O’Gorman says the team worked hard to find a good offsetting partner (they opted for South Pole, which is separate to Verra but uses that organisation’s certification standards). There are active discussions going on about whether these schemes are the way forward for Innocent, she adds.
“Our argument was always that we’d rather not sit and do nothing at all. A lot of decarbonisation targets are going to take time, so at least we can be investing in nature in the short term. Some companies say ‘well, I’m offsetting so I’ve done my job’ – we never saw it like that.
“That’s the challenge of working in sustainability, you think you’re doing the right thing and then everyone learns a bit more and reassesses. There’s no rulebook.”
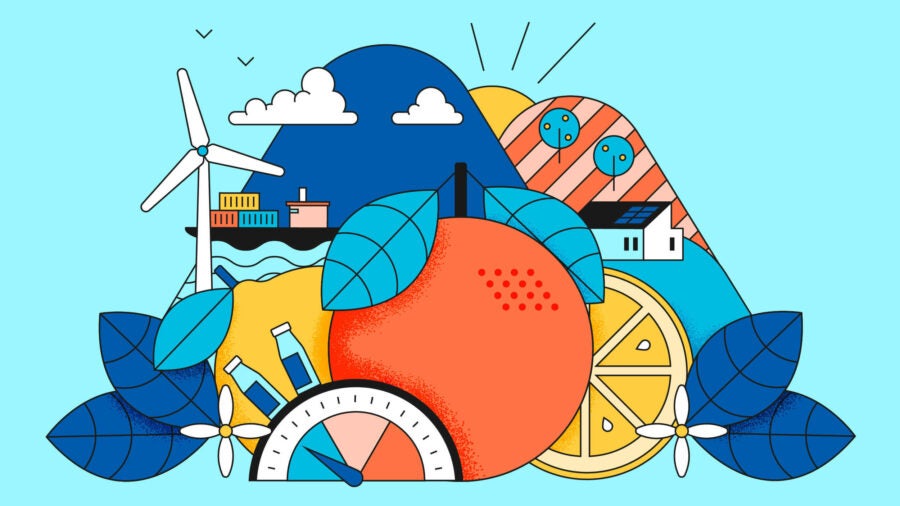
Rotterdam Port is an unlikely spot for a landmark green investment. The largest seaport in Europe stretches for miles in a drab maze of rusted drums, slag heaps and stacks of shipping containers. But on the far side of a scrubby field packed with seagulls pops a familiar halo logo.
It sits atop Innocent Drinks’ new €225m (£198m) factory, dubbed the Blender. Despite its unassuming setting, the factory is packed with technology aimed at making it one of the world’s first carbon-neutral, all-electric drinks factories.
Innocent is a household name in the UK for its colourful, healthy smoothies and juices and quirky branding (its London HQ? Fruit Towers. CEO? Chief squeezer). But the company might be almost as well known for its ethos.