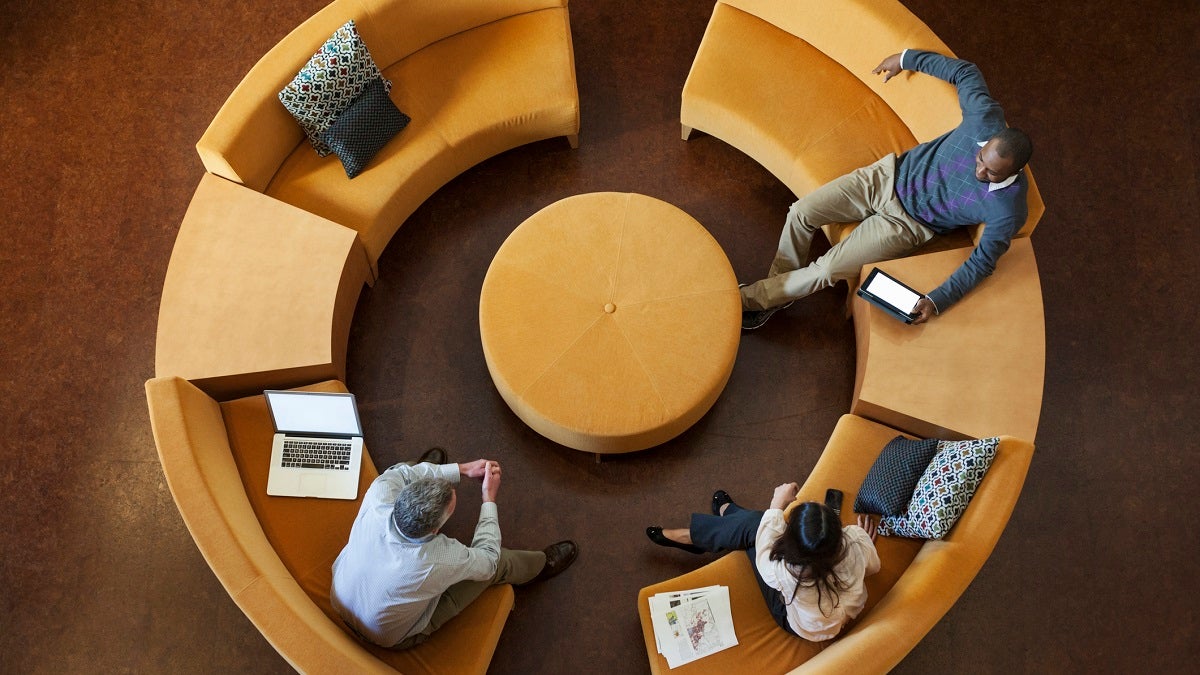
The giants of consumer tech have prospered during the pandemic, with Apple and Samsung in particular announcing yet more triumphant sales figures. But another set of numbers provides an altogether more sobering read: the sector generated a record 53.6 million tonnes of electronic waste in 2019 – up 21% on 2014’s total – according to research published last year by the Global E-Waste Statistics Partnership.
E-waste has become the world’s fastest-growing domestic waste stream – a problem that’s been compounded by increasing consumption, shortening product lifespans and limited repair options, as anyone who’s ever tried to get an old laptop fixed will know only too well. Less than 20% of e-waste is collected and recycled, leaving the rest, much of which contains toxic chemicals, destined for landfill or incineration.
Enabling the circular economy in consumer tech
The environmental impact of e-waste stretches far beyond the toxicity of its components. “During 2020, more than 100 billion tonnes of raw materials were extracted from the earth – the most ever,” says Otto De Bont, CEO of Renewi, a waste-management company operating mainly in the UK and Benelux.
The first goal of Renewi’s five-year sustainability strategy is to “enable the circular economy”. To this end, De Bont explains that there needs to be a dramatic improvement in the recovery of previously used material, such that far more of this can be converted into secondary raw material for new products. He points to recent research published by a Dutch social enterprise called Circle Economy.
“According to its Circularity Gap Report 2021, if the circular economy were to be enacted globally, it would be possible to close the emissions gap and slow global warming. Today the world is 8.6% ‘circular’. But, if governments, industry and other key players were to embrace the circular economy and recycling, as opposed to allowing the incineration or disposal of used material into landfill, they could push the figure up to 17% by 2032.”
The time has come for producers to move towards recycling as the starting point of the development process of new products
But getting the consumer tech industry to cooperate in such an effort will be no easy task. So says Christian Rudolph, a partner at co:dify Group, a Berlin-based innovation consultancy whose clients include Philips and Fairphone.
“The circular economy needs a high level of transparency in the supply chain, but tech companies aren’t always fully aware of what’s happening throughout their supply chains,” he says. “Anything that occurs in their own plants is quite transparent but it’s far less so when you’re talking about a supplier of a supplier. An average mobile phone comprises 250 materials, so it’s simply not viable for those companies to dig that deep into their supply chains.”
Rudolph adds that their supply chains rarely feature the logistical systems that would facilitate the reuse of materials. “When you aren’t planning these into your designs, you really decrease the probability that your product will be recycled,” he says.
According to Rudolph, consumer tech manufacturers need to think more about “precycling”. This means taking recycling requirements into account at the design stage and embracing key circular-economy concepts, such as reducing the number of materials in their products to make these easier to recycle.
Circularity and smartphones
Rudolph acknowledges that some consumer tech firms are starting to take circularity more seriously, although that’s not because they’re worried about the PR risks posed by their contribution to the e-waste mountain.
“The impact of customer scrutiny is limited,” he says. “If we look at recent scandals in the tech industry, they have a very short shelf life – everything tends to return to normal after a couple of weeks.”
They are more concerned about the price volatility of raw materials and want to mitigate that risk, according to Rudolph, but so far they are only touching on “the outer rings of the circular economy. In essence, they are building their phones as they always did, but now they have buy-back systems in place, so that you can return your old handset for scrap. Yet they’re not using those materials to produce new phones.”
One mobile phone producer that’s way ahead of the pack in the circularity stakes is Fairphone, a social enterprise established in Amsterdam in 2013 to make handsets with a lower environmental impact.
A certified B Corporation, Fairphone is also on a mission to ensure fair conditions for those working throughout its supply chain, as unethical employment practices are particularly common in the mineral extraction sector. The company has created a modular, repairable phone, where parts such as the battery can be easily replaced. It has not all been plain sailing for the company. It struggled when negotiating deals with mobile operators, while its first two models were significantly more costly than their mainstream equivalents. But in August 2019 Wired deemed the Fairphone 3+, which is made from 40% recycled plastic and available on Vodafone’s network in the UK, a potential “breakthrough product”.
Rudolph thinks that it would help Fairphone to think first and foremost about making a great product. “It can be circular on the back end, but on the front end it needs to look very compelling to the consumer. Its quality should be at least comparable, but maybe even superior, to that of linear products.”
Even if Fairphone can’t yet compete on quite the same level as the smartphone giants, it is playing an important role by showing what level of sustainability can be achieved in its industry, thereby prompting conversations about circularity among businesses and consumers.
The need for regulation
For De Bont, whose company provides recycled plastics through its Coolrec subsidiary, the only way to prompt consumer tech firms to adopt a circular approach is legal compulsion.
“Although consumers are open to sending their e-waste for recycling, manufacturers are less inclined to draw on that material when making new products,” he argues. “To ensure that electronic goods are created using a mix of primary raw materials and secondary materials, it is important for governments to introduce legislation requiring manufacturers to do so. Governments also need to help align the prices of high-spec secondary raw materials with those of primary raw materials. The time has come for producers to move towards recycling as the starting point of the development process of new products. Currently, it’s the final stage making the e-technology more difficult to process.”
De Bont continues: “The European Parliament has introduced legislation across the EU, but member states’ governments can interpret this individually, making the ‘end of waste criteria’ different from country to country. Consistency in regulation is required if we’re to move towards the circular economy.”
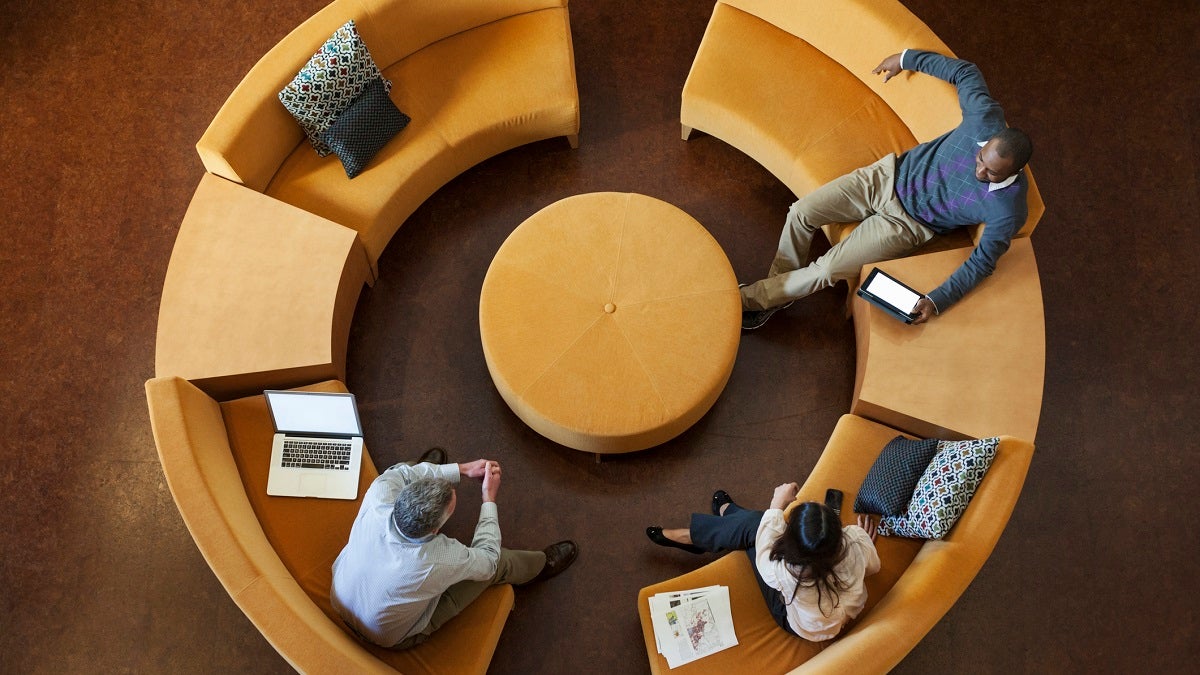
The giants of consumer tech have prospered during the pandemic, with Apple and Samsung in particular announcing yet more triumphant sales figures. But another set of numbers provides an altogether more sobering read: the sector generated a record 53.6 million tonnes of electronic waste in 2019 – up 21% on 2014’s total – according to research published last year by the Global E-Waste Statistics Partnership.
E-waste has become the world’s fastest-growing domestic waste stream – a problem that’s been compounded by increasing consumption, shortening product lifespans and limited repair options, as anyone who’s ever tried to get an old laptop fixed will know only too well. Less than 20% of e-waste is collected and recycled, leaving the rest, much of which contains toxic chemicals, destined for landfill or incineration.