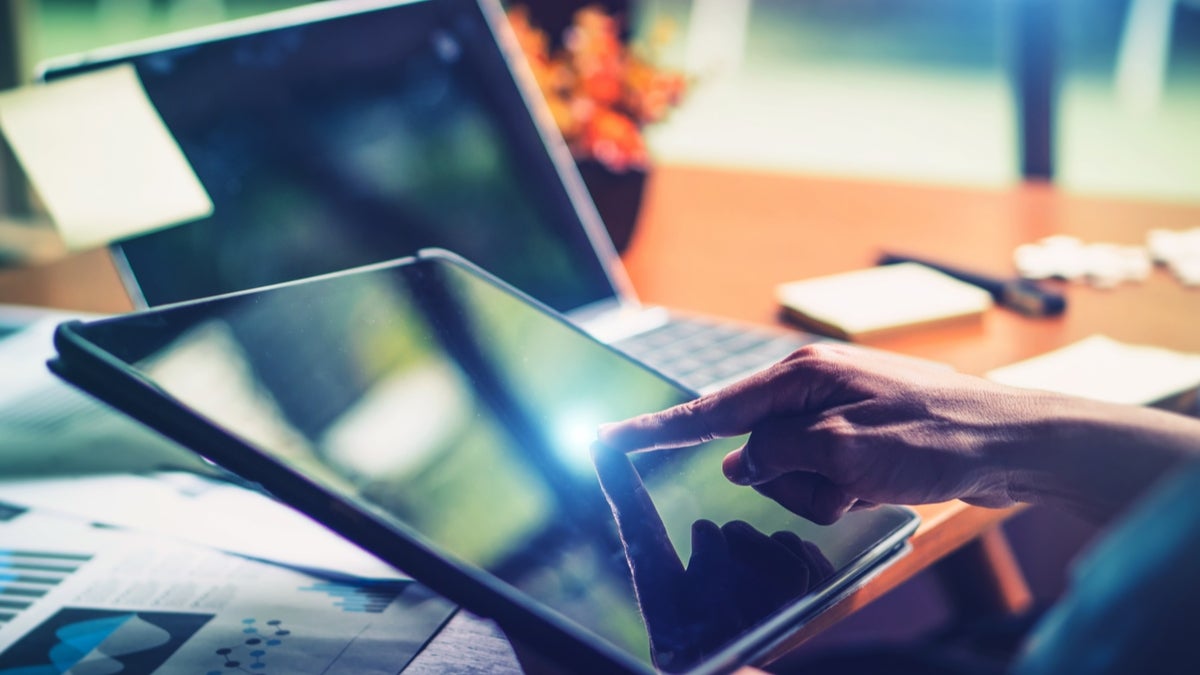
The world has gotten a crash course in supply chain management in recent years. The question now is how do we respond? The cold hard costs and deeply felt impacts of supply chain disruption have elevated the issue as an urgent business priority. The hyper-connected nature of the global economy has meant that, from Covid-fuelled supply shortages to cybersecurity attacks, when supply chains are hit the ripple effects spread fast and far.
So much so that global supply chain disruptions are now costing large companies $184m a year on average, according to a recent study by Interos, the operational resilience company. Nearly all (94%) of the 900 senior IT, security and procurement decision-makers surveyed reported some negative impact to revenue resulting from supply chain disruption. They cited a variety of supply chain risks including cyber breaches, financial risks and ESG (environment, social, governance) transparency issues.
A board-level challenge
Crucially, supply chain shocks don’t just impact revenue and profitability. They can also be damaging to public perception and confidence. 83% of survey respondents reported that their firm has suffered reputational harm as a result of supply chain disruption. Meanwhile, corporate boards are newly focused on what’s happening behind the dashboards, asking the C-suite difficult supply questions 20 to 24 times a year, according to Interos’s research.
“In the past we worked primarily with procurement and compliance teams. Now everyone we partner with at companies are in the C-suite. Supply chain issues are landing on CEO and board desks more so than any time during my 25-plus years in this industry,” says Jennifer Bisceglie, founder and CEO of Interos, whose AI-powered platform maps, monitors and models global supply chains. “But also, for the first time, ordinary people are talking about supply chain problems. The Covid-19 crisis meant they couldn’t get vital cleaning supplies and toilet paper. That suddenly made it personal.
“There’s growing acknowledgement that every business is only as strong as its supply chain. It’s the fundamental enabler of any company’s mission, day-to-day operations and long-term growth agenda. If you look at what’s happening with ESG goals, too, executive compensation is now being tied to supply chain metrics. There’s heightened awareness of just how important these unseen global networks are to a business.”
Though the fragilities exposed in supply chains during the pandemic were stark, it’s important for organisations to realise, and explicitly acknowledge, that those supply chains performed how they were built to operate – short, tight and just in time. The flaws in traditional supply chain processes, which significantly lack visibility, were evident previously, but it took a black swan event in the form of a global pandemic to finally break them.
Optimising at ‘click speed’
Designed for efficiency at the cost of fragility, the breaking of global supply chains now presents an opportunity to rebuild them for strength, agility and resilience. We’ve seen the extent to which markets rely on supply chains not just to deliver products – but to stabilise and secure the wellbeing of people’s livelihoods. Truly resilient supply chains that thrive in a hyper-connected economy can’t be achieved overnight, however. Building a safer and more secure global economy requires an intellectual, cultural and government policy shift. It must be led from the top as a board and government priority with shared responsibility across the C-suite and national leadership, alongside investment in the technologies that power intelligent supply chains.
“Supply chains must be continually optimised at ‘click speed’ because that’s how events and customer demand happens globally. Supplier relationships are extensive, connecting one company to the next across multiple layers. Understanding how to track and leverage that hyper-connectivity as a strength is key,” says Bisceglie. “Ultimately, these vast networks are a big data problem. They’re not something that can be analysed by humans any more using annual surveys or other manual tools. The solution comes down to artificial intelligence. It’s a 24-7 technology with no lag time that can process large data sets so organisations can see and pre-solve disruptive incidents.”
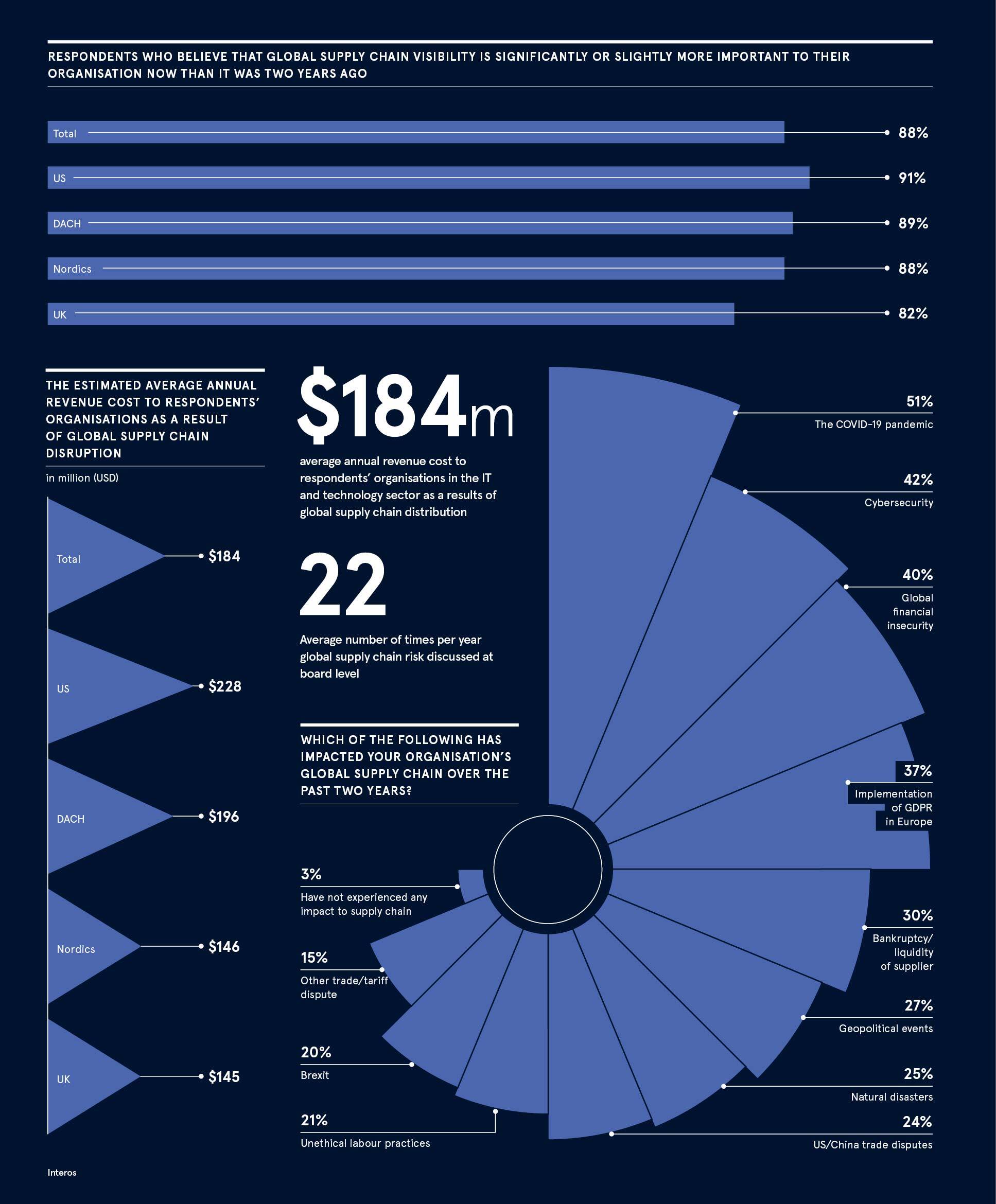
Powered by AI and machine learning, Interos is reinventing how organisations manage their supply chains through the company’s Operational Resilience Cloud. It can model the entire ecosystems of complex businesses, down to any single supplier, into a living global map. By vastly enhancing visibility across the supply chain, Interos helps reduce risk and avoid disruption, while also uncovering new opportunities for companies to benefit from supplier relationships.
Mapping the sub-tier
The technology not only continuously maps sub-tier relationships in an organisation’s supply chain, but also monitors global events that might impact their business. Using AI, it helps organisations understand who is in their supply chain, the implications of those relationships, and whether any actions are required.
“We do that every day – map, monitor and model,” says Bisceglie. “The core idea from an operational resilience perspective, is to be able to pre-solve or pre-empt costly disruptions. Over the last 18 months with Covid, we discovered the true threat posed by concentration risk, an over-reliance on certain organisations or countries. It also laid bare the financial instability of our supply chains.
“You can also look at global cyber breaches, such as SolarWinds, where an attack on one rapidly became a breach of global proportions. Or consider the Suez Canal crisis, which demonstrated the enormous global impact of a single ship stoppage. When one of these activities occurs we need the ability to understand how it affects our supply chains and what to do, in real time. The future of the supply chain is true operational resilience. That means pre-planning for disruptions so that when the unexpected happens, you already know how to respond. The companies that understand and act on this intelligence will be at an advantage.”
Bridging the gap
Jennifer Bisceglie, founder and CEO of Interos, which recently gained ‘unicorn’ status following its Series C funding round, outlines the importance of diverse leadership
Your company has thrived during a period of inability. What advice do you have for other leaders still working through hard times?
Our success is based on focus. The company is 17 years old. Like any startup, we’ve overcome challenges to get to where we are. We’ve always stayed singularly focused on solving the problem of transparency in the supply chain to help organisations pre-solve problems and create more value from their relationships. Some entrepreneurs suffer from ‘shiny penny syndrome’, where you’re constantly distracted by new ways to grow revenue.
My advice is to maintain focus and have the fortitude to understand you’re on the right path and solving a real problem. When I graduated college, I was introduced to the nexus of technology and supply chain, and I identified a clear gap. Everyone was focused on technology within the supply chain and within the company but not between businesses themselves. Those relationships have important implications for who can ultimately access your products or services. We never lost sight of that gap.
As one of the few female founders who has built a unicorn business (valued at over $1bn), what would you say to other women aspiring to that success?
I’m a big fan of the saying ‘if you can see it, you can be it’. The fact that Interos was able to achieve unicorn status comes down to two things. One is realising this is just the beginning of our journey. It’s certainly not the end. Being a unicorn comes with significant responsibility to build and grow your valuation. The second thing, for the leaders coming after us, is now you know it’s possible. Surround yourself with true believers in the mission and appreciating the fact that this can happen to you is important. I just wanted to be the best leader, female or otherwise. I truly believe that we all have that opportunity.
What should other tech companies be doing to bridge the gender gap?
We’re seeing different countries and companies globally passing laws to enforce diversity benchmarks, which is positive. These actions must be purposeful and supported by defined tracking processes. I believe if you can’t find the right candidate for a role, you should be thinking about how to create a pipeline, outside of your traditional channels if necessary, so you can educate, elevate and mentor the diversity into that role.
There are multiple ways to get at diversity and it can’t simply be a compliance activity. Diversity of people, experience and thought strengthens companies and drives innovation. It’s an ongoing goal, not a one-time activity. It’s incumbent on all of us and it’s something we take very seriously at Interos. We have a target of a 50-50 gender split by 2025. We measure that in our quarterly board meetings. Even though we’re not a big company we believe in it and have set that mandate.
What are your thoughts on the growing concerns over ethical supply chain behaviour – are we really poised for change?
We’re starting to see change, not least because there are now executives in listed companies whose compensations are directly tied to ethical supply chain behaviour. We’re seeing that top-level story in the press, but I think the follow-up audit and execution still needs to be reported on. It’s moving in the right direction, however.
I also think it’s interesting, as you look around the world, that different regions define it differently. In EMEA we typically see emphasis on carbon footprint. In Africa, child labour is a chief concern. And in the United States it’s more focused on supplier diversity. Giving different regions the power to make an impact is so important, and measuring and reporting their gains is just as essential.
We’re also seeing progress when companies are ready to go public. Ethical supply chains are no longer given passing mentions in 10-K filings; it’s something companies analyse and report out. Supply chains become a source of competitive advantage as companies invest in them.
There’s increasing exposure at the retail level as well. Many websites, especially consumer sites, allow people to understand the exact provenance of a sneaker or their coffee beans. Think about how that empowers them. They’re able to drive ethical sourcing and supply chain transparency by buying into companies who prioritise it. We’re going to see much more of this transparency underpinning company reputation and performance in the future.
Supply chain disruptions cost organisations an average of £134m annually. For more information on how you can eliminate this cost, reduce risk, avoid disruptions and achieve superior enterprise adaptability, visit Interos.ai
Promoted by Interos
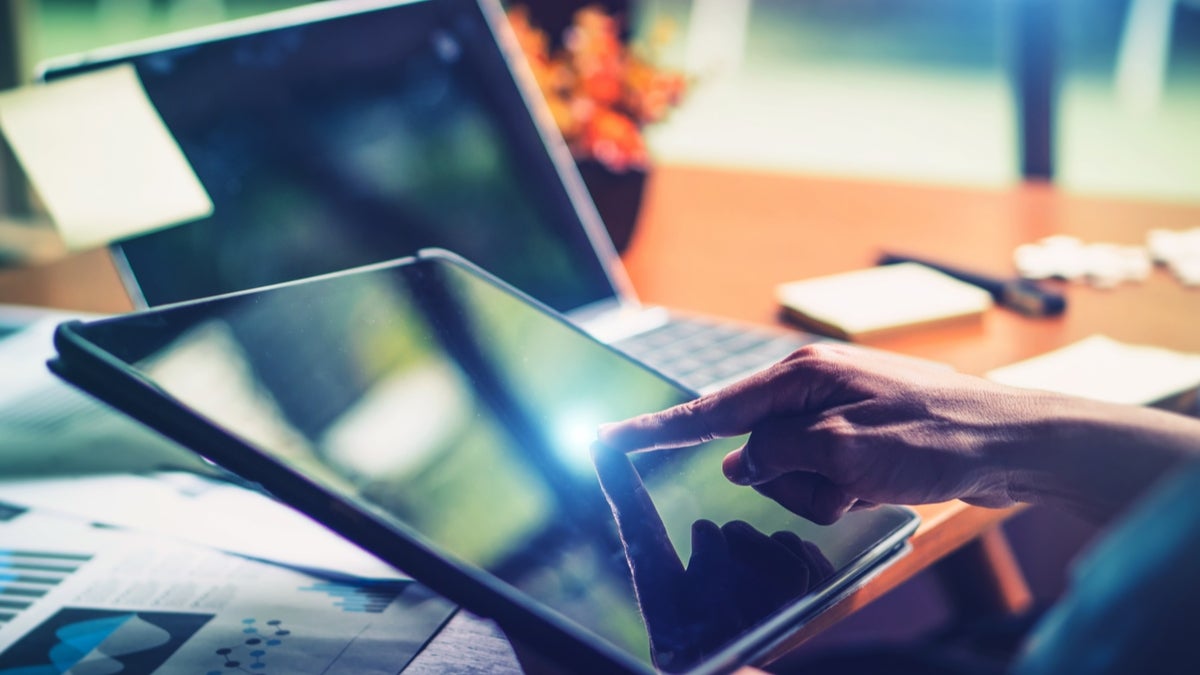
The world has gotten a crash course in supply chain management in recent years. The question now is how do we respond? The cold hard costs and deeply felt impacts of supply chain disruption have elevated the issue as an urgent business priority. The hyper-connected nature of the global economy has meant that, from Covid-fuelled supply shortages to cybersecurity attacks, when supply chains are hit the ripple effects spread fast and far.
So much so that global supply chain disruptions are now costing large companies $184m a year on average, according to a recent study by Interos, the operational resilience company. Nearly all (94%) of the 900 senior IT, security and procurement decision-makers surveyed reported some negative impact to revenue resulting from supply chain disruption. They cited a variety of supply chain risks including cyber breaches, financial risks and ESG (environment, social, governance) transparency issues.