These days our information, communication and entertainment are all delivered digitally, often in a timeframe that would have been thought impossible just a few years ago.
Digital is light, quick, clean and, above all, convenient; attributes not often associated with an industry like manufacturing. Manufacturing is tactile and has a weight to it. There are time and labour costs involved in delivering physical parts that have put it in a category of its own while the digital revolution rages on.
Indeed, for more than 150 years, injection moulding has been a linchpin of the manufacturing world, making it economically possible to deliver large quantities of the exact same part through precise tooling. But while this manufacturing approach works well for the applications it is suited for, it is not well suited for all.
First and foremost, the design must not be so overly complex to rule out tooling. Further, the design cannot evolve or else the tooling must also change, triggering added expenses in downtime and rework. And, finally, the total quantity of parts required must be high enough to recover the immense costs in time, resources and physical space that are inseparable from tooling.
3D printing continues to drive digital technology further into the manufacturing arena, reshaping the process and economics of delivering production parts. Frequently referred to as rapid prototyping, due to its widespread use for quick prototypes, 3D printing is also known as additive manufacturing; a succinct label that defines the process of building geometries layer by layer.
This additive process is of central value to design and engineering teams, as it frees them from the persistent constraints of tooling to enable greater design complexity and efficiency than ever before. Yet the floodgates restraining custom products and efficiency-enhancing designs have given way only slightly, and are still being held up in the three key areas of speed, cost and materials.
Now, though, a new production platform for additive manufacturing has solved all three, introducing a radical departure from the 3D printing and manufacturing technologies that have come before it.
The Figure 4 platform from 3D Systems, based on a 30-year-old stereolithography (SLA) configuration patented by the company’s co-founder Chuck Hull, combines the design freedom of 3D printing with speed, throughput, effective total cost of operation, and capacity to deliver greater agility and capabilities to mass custom manufacturing.
This new additive manufacturing platform can be integrated into automated assembly lines and scaled with ease in any configuration of printing modules. Secondary processes, such as material recovery, washing, curing, finishing and inspection, can also be integrated and optimised with downstream workflows.
This new additive manufacturing platform can be integrated into automated assembly lines and scaled with ease in any configuration of printing modules
Up to 50 times faster than current 3D-printing systems – in benchmarking tests an automotive vent achieved a cycle time equivalent of 95 seconds – the platform is also modular and can be fully automated, allowing for the production of unique configurations from a single print engine to high-volume production systems comprised of many multiples of engines.
These part production speeds, along with features such as automated material delivery, in-line manufacturing capabilities and integrated post-processing, present a disruptive alternative to traditional injection-moulding manufacturing without the exorbitant cost of tooling. The Figure 4 platform also enables the use of more reactive plastic resins, which allows the platform to create parts in hybrid materials with properties that rival traditional injection moulding.
With high throughput, leading total cost of operations and expanded material options that can serve a broader range of end-use applications across industries, 3D Systems is now working with strategic partners and industry experts to develop specific solutions to benefit a wide range of sectors, including the healthcare, aerospace, automotive and durable goods industries.
“Productivity, repeatability, durability and total cost of operations are top of mind for our customers,” says Vyomesh Joshi (VJ), president and chief executive of 3D Systems. “We believe our breakthrough Figure 4 platform will deliver real 3D-production solutions and competitive advantages to answer our customers’ needs, and transform manufacturing of both mass customised and complex end-use parts across key verticals and applications.”
To find out more about the Figure 4 platform please visit https://www.3dsystems.com/
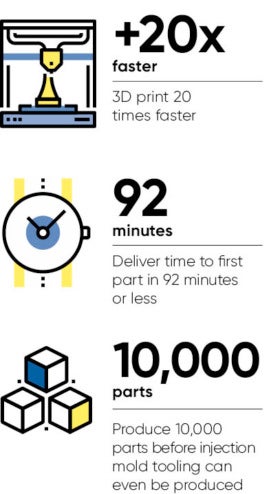