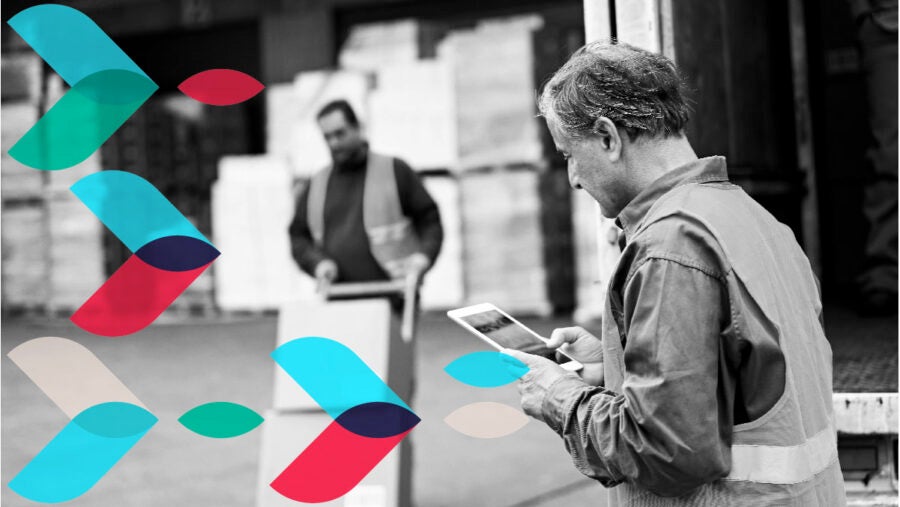
If 2020 broke the supply chain, 2022 certainly wasn’t the year it got fixed. From a shortage of materials, labour and skill to disrupted logistics, many of the same challenges continue to plague supply chains. Pent-up demand is leading to blockages and global conflicts such as the war in Ukraine are pushing up prices, but this, some experts say, was inevitable.
After 30 years of trying to make the global supply chain as lean as possible, the case for savings, efficiencies and just-in-time strategies no longer stands up. “The global supply chain is too long,” says James Rickards, bestselling author of SOLD OUT: How broken supply chains, surging inflation and political instability will sink the global economy. “When you have that many moving parts, it breaks under its own weight.” All the plans put in place by supply chain managers served to cut down on inventory, time and effort but failed to take into account the hidden cost, says Rickards. “And the hidden cost was that you made this thing extremely fragile and frail, not resilient or robust.” 2023 is the year to try something new.
Making sustainability priority number one
One of the biggest risks facing any business is climate change, and this has particular ramifications for supply chains. Extreme weather conditions can lead to material shortages as food, wood and mineable materials are harder to harvest or access. Floods, fires and storms can upset logistics too, causing delays or losses. All of this means becoming greener needs to be high on the priority list, says Neeral Shah, the CEO and founder of YardLink, a B2B marketplace focused on digitising the supply chain for construction.
“There is a push towards making sure your supply chain is green and sustainable,” he says. “It’s important to look at your sustainability goals and think about your supply chain differently.” Shah recommends companies consider partnering with specialists who have sustainability accreditation and expertise to manage ESG goals for 2023.
Bringing supply chains closer to home is another way to make them greener. “There is always a local supply chain that’s readily available,” says Shah. “That helps to reduce prices and with logistics. But when you also consider the carbon footprint of having things delivered from hundreds or thousands of miles away and bringing it down to 10, 20 or 30 miles away, that makes a huge difference.”
Relocating the supply chain
Covid highlighted the fragility of long, global supply chains. As countries, particularly China, shut down in 2020, companies like Jaguar Land Rover resorted to flying parts over in suitcases as they became harder to source. For this reason, many brands are exploring the possibilities of more localised supply chains in 2023.
The global supply chain is too long. When you have that many moving parts, it breaks under its own weight
“Globalisation failed because we stressed the supply chain too much. It became too long,” says Rickards. He thinks that in 2023, and beyond, brands will become far more selective about which countries they do business in and with. A “college of nations”, as Rickards terms it. “What we will have is a new world where we will trade with our friends but many countries won’t be in the club,” he says. “Certain groups will trade with each other, outsource to each other, but China won’t be in this club. Anyone not in the club will have to go their own way.”
Supply chain managers will need to seek out new partnerships as sources of raw materials and, wherever possible, find what is needed nearby. It also means that organisations will have to get much smarter about information sharing.
Digitising the supply chain and boosting connectivity
YardLink analysis found that two of the largest construction sites in London receive up to 100 deliveries from all over the world, every week. To combat this, says CEO Shah, companies should look to digitise so that projects in any given region can look to make better use of resources. “Digitisation helps you communicate with different stakeholders across projects. You can work with partners or third parties and ask whether a locally available asset is available and if it is, then why not use it instead of sourcing further away and dealing with the extra logistics?”
Keeping track of all the assets in a supply chain is easier using an application programming interface or API. It boosts connectivity through the whole supply chain, helping suppliers’ systems (and those of the suppliers’ suppliers) talk to one another. The internet of things (IoT) is another important game-changer for supply chains in 2023, says Shah. Whether an organisation is in the manufacturing sector or the food industry, every supply chain will involve hundreds of individual items of machinery and technology. IoT allows supply chain managers to gauge the health and performance of each item as well as helping to track them on the move.
“Once you have telematics on board you can measure fuel emissions, understand an item’s location, see if it’s in use or idle,” Shah explains. “This all helps to reduce costs and tackle carbon emissions, as a lot of carbon is emitted just from equipment sitting idle on site.”
But IoT has its drawbacks too, notes Charles Eagan, CTO of BlackBerry. “The problem is that there are so many millions of endpoints,” he says. Throughout the supply chain these endpoints could vary from an IoT sensor to a piece of smart factory tech to a simple camera. Eagan notes that greater supply chain connectivity and visibility increase a business’s vulnerability to cyber threats.
“All companies will find all kinds of devices are being attacked. So keeping an inventory of what’s being attacked and what could be attacked is job zero.” As with almost every technology-adjacent role in a business, in 2023 supply chain managers will need to balance performance and productivity with security. For this reason, many would be wise to think about hiring cybersecurity roles into the team to protect an optimised supply chain.
Tackling the labour and skills shortage
Technology can also help to fill the gap left by a lack of supply chain talent. “We do need more cyber talent,” says Eagan, “but really I think it’s a technology-people gap. We need to make technological tools easier to use so we can take the simple stuff away from humans and give it to computers.”
This talent gap can be felt throughout the supply chain and it’s one of the biggest risks for 2023. “It’s impacting the entire chain from the trucking industry to the manufacturers. Labour shortages are huge,” says Shah. “You need to look at ways to digitise your supply chain. Automate any processes you can to reduce your reliance on labour and get the information you need faster.”
International supply chains have been badly damaged but 2023 may be the year they start to recover. The key, says Rickards, is not to try to rebuild them in their former image. “When you break a wine glass and it shatters into 5,000 pieces, you don’t try to put it back together. You find a new glass.”
The successful supply chain of 2023 will use connective technology, have an understanding of the geopolitical climate, keep an eye on sustainability, and use the finest talent available. Any supply chain managers who fail to take these things into account may find themselves stuck in 2022.
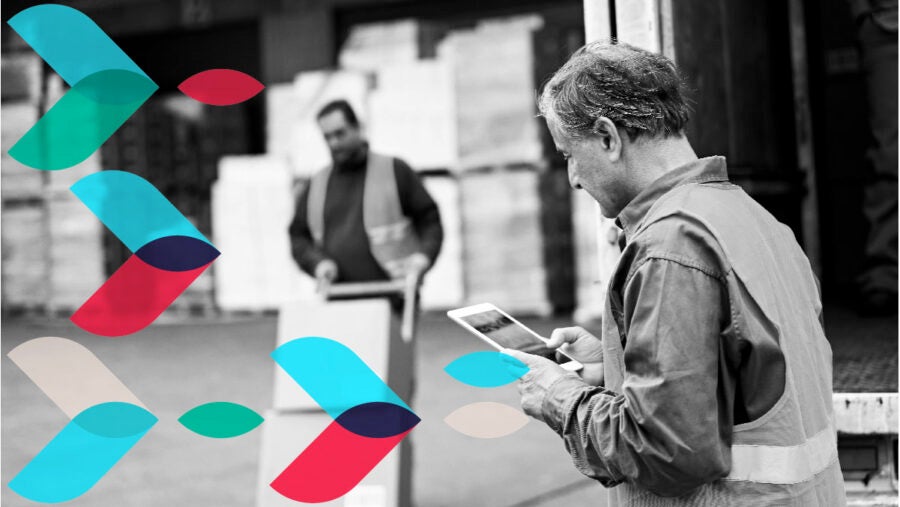
If 2020 broke the supply chain, 2022 certainly wasn’t the year it got fixed. From a shortage of materials, labour and skill to disrupted logistics, many of the same challenges continue to plague supply chains. Pent-up demand is leading to blockages and global conflicts such as the war in Ukraine are pushing up prices, but this, some experts say, was inevitable.
After 30 years of trying to make the global supply chain as lean as possible, the case for savings, efficiencies and just-in-time strategies no longer stands up. “The global supply chain is too long,” says James Rickards, bestselling author of SOLD OUT: How broken supply chains, surging inflation and political instability will sink the global economy. “When you have that many moving parts, it breaks under its own weight.” All the plans put in place by supply chain managers served to cut down on inventory, time and effort but failed to take into account the hidden cost, says Rickards. “And the hidden cost was that you made this thing extremely fragile and frail, not resilient or robust.” 2023 is the year to try something new.