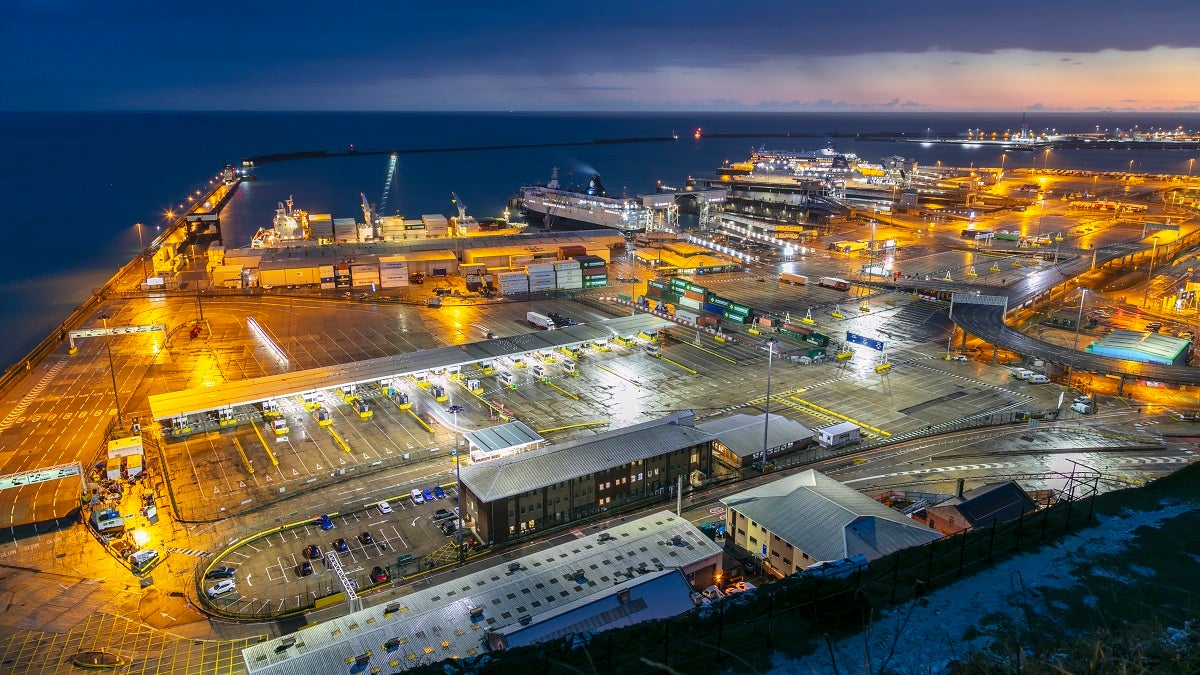
Leaving the EU meant the end of free trade between Britain and its European neighbours, along with an end to the free movement of goods, services and people. For many companies, especially manufacturers that rely on European partners for components, this has led to inevitable supply chain upheaval.
John Breen, geopolitical consultant for strategic advisory firm Sibylline, says the main challenges for manufacturing businesses in the wake of Brexit include trade barriers, exacerbated labour shortages, increased logistics costs and tariffs.
“Brexit is having a negative impact on UK export-focused industries like manufacturing,” says Breen. “The new customs rules as of January 2022 have increased operating costs for the UK’s manufacturing industry.”
Increased costs and paperwork are the main effects on supply chains for manufacturers who import components from the EU, as well as those who did enjoy free access to EU markets for export. Breen says this is significant because the EU accounts for 42% of all UK exports, so extra costs on the distribution side of the supply chain are unavoidable for British manufacturers.
Working with UK manufacturers, this has had a huge impact on our carbon neutral status
“In goods alone, the majority of the UK’s top 10 export and import partners are in the EU,” says Breen. He adds that the UK services sector “has not experienced as much disruption to date as London remains an important European financial hub”.
A recent report on tackling carbon emissions and trade policies, by the UK Trade Policy Observatory and Centre for Inclusive Trade Policy of the University of Sussex Business School, recommended a comprehensive approach to supporting decarbonisation on a global level. Both the UKTPO and CITP support low-carbon supply chains. At government level, the report recommends green investment, climate finance, technology transfer and cooperation in the development of international standards for reducing emissions on supply chains. In the meantime, though, British companies are taking matters into their own hands to reduce the carbon footprint of supply chains outside the EU single market.
Tim Warrington, CEO of robotics company Servicerobots, says the firm sources all its components within the UK. “And if we can’t source from within the UK, we try to manufacture components ourselves, which means a low carbon footprint,” he explains. As well as the green benefits, he reports long-term financial and quality control benefits from keeping supply chains within the UK. “If there are any quality issues, we can make adjustments very fast, which saves in waste,” he says.
“After the initial set-up of tooling, producing parts ourselves is around 80% cheaper than buying them in,” he explains. “It helps us cope with costs incurred by Brexit. Companies that take this approach are helping to increase manufacturing in the UK to cope with demand.” Warrington describes operating outside the EU as “challenging because of the usual red tape to get parts but, like anything in business, you just have to get over the hurdles and make the most of the positives, such as increased demand for parts made in Britain, which are now harder to source in Europe.”
Like anything in business, you just have to get over the hurdles and make the most of the positives
Kanzen Skincare also reports advantages of not relying on EU suppliers. Like Servicerobots, David Connor, joint CEO of Kanzen Skincare, says the company sources “100% of our components from the UK. As a startup, it was vital for our development and brand to act fast and talk to UK suppliers if we need them,” he explains. Keeping supply chains for components within the UK is also important for the company to meet its sustainability goals. “We’re carbon-neutral – and the first cosmetic company to achieve plastic neutrality in oceans,” he says. “Working with UK manufacturers has had a huge impact on our carbon-neutral status.”
Connor agrees with Warrington that costs may be linked to keeping supply chains within the UK. For Servicerobots, it was readying the factory to make more parts onsite, while Kanzen says that UK manufacturers can be more expensive.
“But as a premium skincare brand we’ve factored in these costs – and the speed and ease throughout the supply chain outweigh the change in costs,” explains Connor. He is clear that keeping supply chains within the UK has also helped manage costs incurred by Brexit. “We find it easier to manoeuvre regulations in the UK since Brexit. Our only challenge is the export of goods to European countries because the export regulations are tighter plus we pay double for registration of products,” he says.
Companies such as Servicerobots and Kanzen Skincare are taking the initiative in greening supply chains by bringing them within the UK’s borders wherever possible – although cost benefits can vary and distribution to the EU is more expensive than it was. Private companies can – and often do – take direct and positive action before legislation is in place or government climate policies have caught up with the need for change.
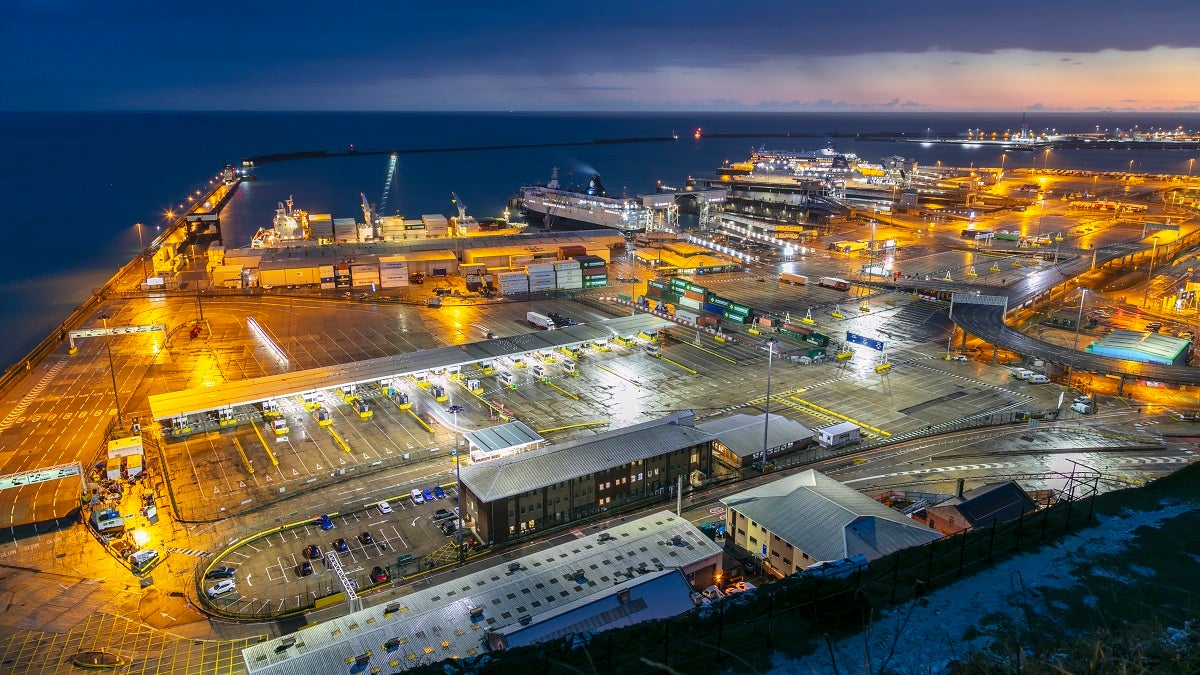
Leaving the EU meant the end of free trade between Britain and its European neighbours, along with an end to the free movement of goods, services and people. For many companies, especially manufacturers that rely on European partners for components, this has led to inevitable supply chain upheaval.
John Breen, geopolitical consultant for strategic advisory firm Sibylline, says the main challenges for manufacturing businesses in the wake of Brexit include trade barriers, exacerbated labour shortages, increased logistics costs and tariffs.
“Brexit is having a negative impact on UK export-focused industries like manufacturing,” says Breen. “The new customs rules as of January 2022 have increased operating costs for the UK’s manufacturing industry.”