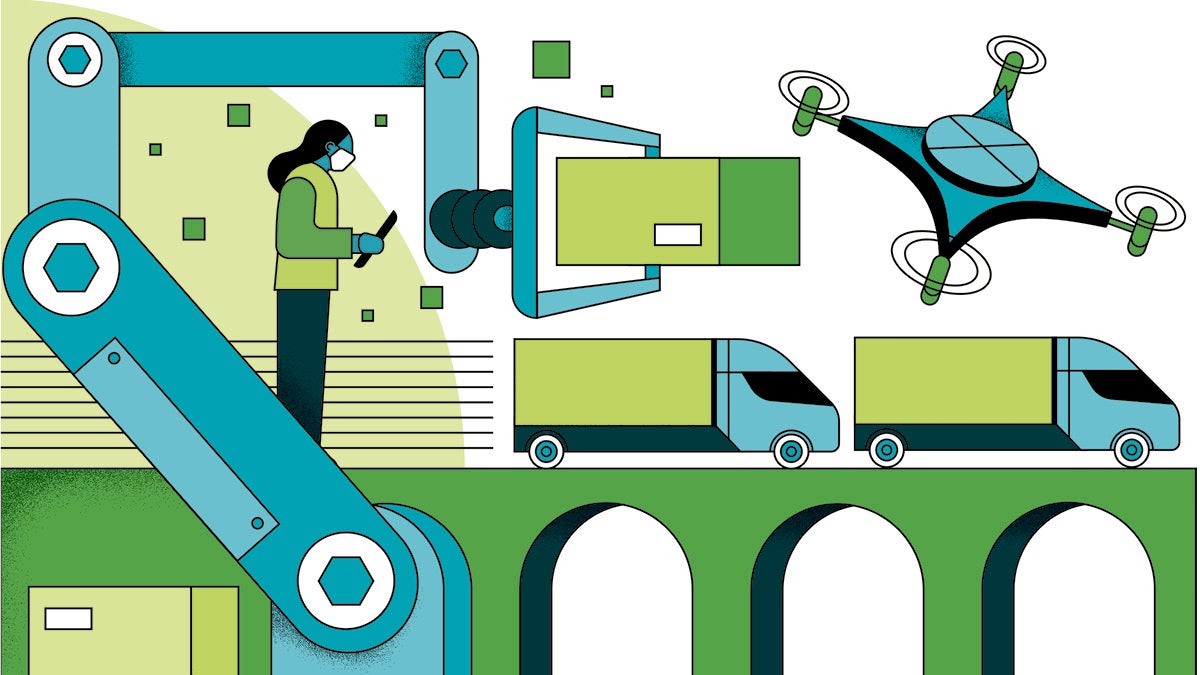
The traditional vision of the future warehouse, where shiny drones zip up and down high bays, speedy robots pick goods with humanoid arms and staff navigate aisles with advanced smart glasses, is certainly both a compelling and feasible prospect. But has the unforeseen arrival of a pandemic threatened the evolution of this supply chain utopia?
The acceleration of warehouse technology
The short answer is no. New requirements in place to curb the spread of the coronavirus, such as social distancing and reduced labour forces, alongside the need to handle snowballing demand, have actually accelerated investment in the future warehouse, with all its tech-powered bells and whistles.
Supply chains have had no choice but to rely on smart technology to ensure better standards of hygiene, fill the labour gap and cope with increased inventory levels.
“The ramp-up of innovation we’ve seen over the past six months prompted by COVID-19 would in normal times have taken years,” says Ian Keilty, chief operating officer at Wincanton. “Having experienced both supply and demand shocks, many customers are looking to technology to make their supply chains more responsive, particularly to meet increased online demand.”
Technologies of the future warehouse
Existing trends, which have been magnified by the pandemic, hint at the kind of technologies likely to shape the future warehouse.
“There was already a move away from utilising core labour to carry out some of the more indirect activity in the warehouse environment, such as moving empty pallets or pallet layering, and the pandemic has increased the focus in this area,” says Angela Howard, vice president of operations, retail and consumer, at DHL Supply Chain. “For example, we’re looking at robotic arms and autonomous trucks to support and work alongside our warehouse colleagues.”
She says that from a safety point of view, the future warehouse is expected to continue to focus more on technologies that enable social distancing, such as robotics, automation, widespread use of sensors and the internet of things.
“Similarly, in the manufacturing space, we are seeing new technologies like fully automatic very narrow aisle robotics being introduced, which can pick and put away full pallets without any human resource, allowing space in the warehouse to be maximised, and health and safety risk minimised,” says Howard.
We are seeing new technologies like fully automatic very narrow aisle robotics being introduced, which can pick and put away full pallets without any human resource
Ocado has relied on data from warehouse management technology to handle increased demand. “While demand at the height of lockdown was off the chart, our Erith [south-east London] facility ramped up to process over 110,000 orders a week, compared with 80,000 just a few months earlier,” says Alex Harvey, engineering director for handling robotics at Ocado Technology. “We used our warehouse system data for quick, adaptive decision-making to squeeze new levels of optimisation out of things like van space.”
During lockdown the company temporarily delisted bottled water, which is heavy and bulky, enabling Ocado.com to make 6,000 more deliveries a week.
“There is increased interest in technologies that make existing warehouses smarter, such as robots that can travel safely around warehouses and work with the people in those environments to get more product through the same space, rather than having to invest in a brand new site before making a start on building the warehouse of the future,” says Keilty. “We are working with our customers to use artificial intelligence on the increasing amounts of data to make the decisions about when and where the warehouses of the future need to be.”
Wincanton is also looking at digital twins, or digital replicas, of the supply chain. “With digital twins we can ask questions of the data and evaluate different operating strategies before investing tens or even hundreds of millions of pounds in future supply chains,” he says.
Team management, flexible working & collaboration
Not all the impacts of COVID-19 on the future warehouse relate to futuristic equipment or flashy digital technologies. The pandemic is also likely to prompt a whole new way of addressing team management and engagement.
“Aside from the advances in robotics, automation and smart technology that will no doubt continue, we expect to see the future warehouse to look very different in terms of the structure of the day and the overall approach to flexibility and shift patterns,” says Howard.
COVID-19 has encouraged businesses to think differently about how they manage their workforce, including how they think about talent engagement and training. DHL has seen an acceleration in the adoption of new innovations in response to this.
“The pandemic has allowed the world of work as a whole to see how things might be done differently, with flexible working now adopted far and wide, and many enjoying a much-improved work-life balance as a result,” adds Howard. “The same can be true for those working in warehouses, whether that might be looking at two-hour shifts, changing the shift patterns offered to people or flexing and adapting the patterns to suit each employee.”
Another likely feature of the future warehouse is space sharing and collaboration. Tony Mannix, chief executive of Clipper Logistics, expects increased collaboration and partnerships in a post-pandemic world, with dedicated shared-user warehouse and transport solutions that can provide cost-efficient warehousing and advanced stock management systems
“This could allow physical and online retail to run seamlessly alongside each other, creating new routes to market and competitive costs, and provides scalability, while reducing congestion and final-mile deliveries,” he concludes.
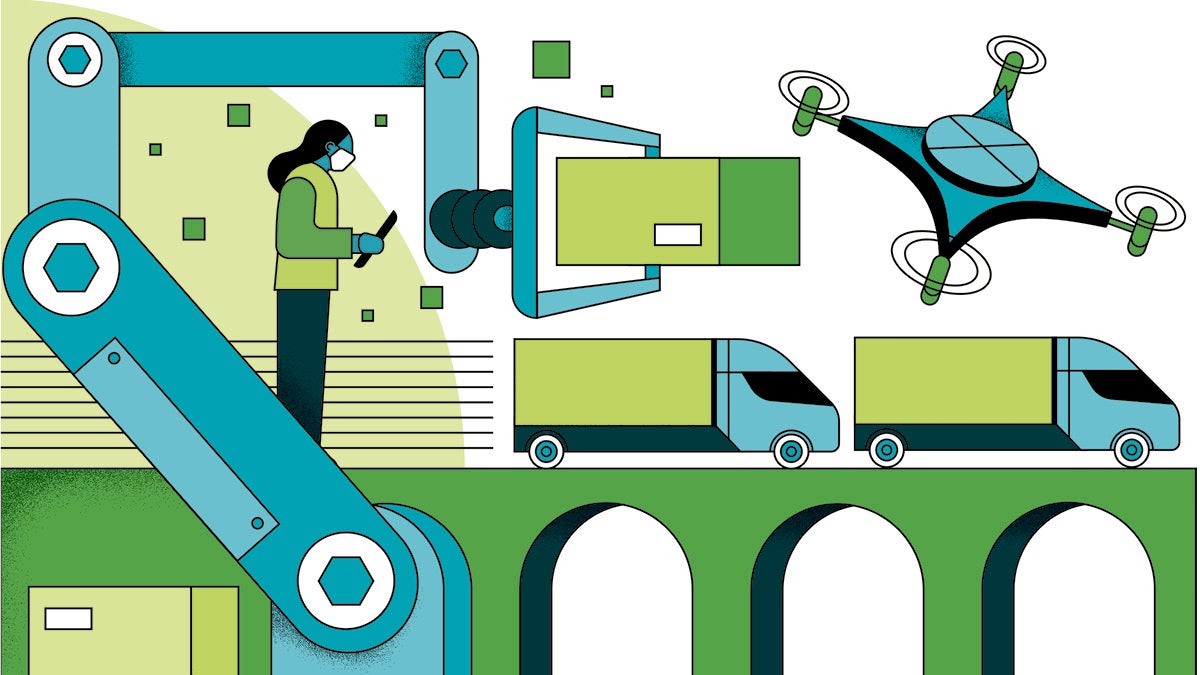
The traditional vision of the future warehouse, where shiny drones zip up and down high bays, speedy robots pick goods with humanoid arms and staff navigate aisles with advanced smart glasses, is certainly both a compelling and feasible prospect. But has the unforeseen arrival of a pandemic threatened the evolution of this supply chain utopia?
The acceleration of warehouse technology
The short answer is no. New requirements in place to curb the spread of the coronavirus, such as social distancing and reduced labour forces, alongside the need to handle snowballing demand, have actually accelerated investment in the future warehouse, with all its tech-powered bells and whistles.