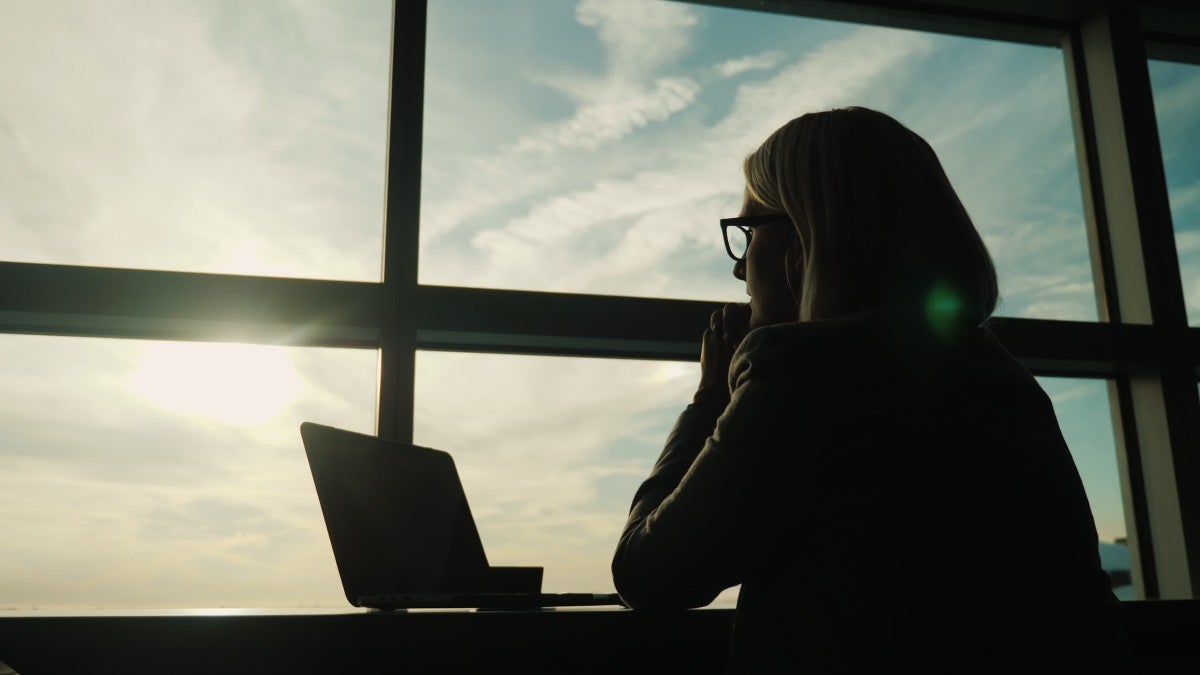
If the Covid-19 pandemic, geopolitical tensions and supply chain disruptions have taught manufacturers one thing, it’s to prepare for the unexpected. So, could cloud computing hold the key to resilience?
“The events of the past couple of years have put considerable pressure on the manufacturing sector to maintain production and keep supply chains and economies moving,” says Dr Phani Sistu, internet of things solutions lead at Hitachi Vantara, which offers storage solutions for businesses. “At the same time, manufacturers have had to deal with workforce challenges and supply and demand fluctuations.”
In pre-pandemic manufacturing conditions, just-in-time was the default model: a workflow system where parts are sourced as close to production as possible in order to meet customer demand without holding excess inventory.
Some fortunate manufacturers with the necessary capacity were then able to pivot to a just-in-case model, in which they build a buffer of inventory to fall back on in the event of supply chain delays.
This can work well in a sector such as the automotive industry, where margins are generally relatively healthy. However, in an industry like healthcare, which runs on thin profit margins, manufacturers aren’t usually in a position where they can afford to hold inventory.
But the pandemic has also highlighted the vulnerabilities of healthcare relying on a just-in-time model. Hospitals struggled to get their hands on ventilators for Covid-19 patients, for example.
Even with the worst of the pandemic now seemingly over, companies still face challenges. In the medical device sector, for instance, the ongoing semiconductor shortage has meant lower levels of production. These manufacturers also find that they’re competing with many other industries for a limited supply of inventory.
Meanwhile, manufacturers that can get their hands on chips are likely paying more because of the sharp rise in prices of raw materials, as well as rising shipping costs. On top of this, the medtech sector is facing a staffing shortage, according to market research from Informa.
If a just-in-time model is to be effective in the future for an industry like healthcare, then, every process in that supply chain needs to be joined up and synchronised. That’s where the cloud comes in: helping to build those connections.
By adopting cloud-enabled technologies, medical device manufacturers could keep on top of challenges resulting from staff and supply shortages, especially when it comes to distribution and inventory management.
Moving to the cloud allows for better interoperability between different business units by dissolving data silos
Manufacturers should consider moving supply chain operations to the cloud as it enables them “to use real-time data to create contingencies”, says Pierre Liautaud, an member executive council at Aim10x, a group of business leaders encouraging digital transformation in supply chains.
The cloud can bring together data from an array of technologies “that support manufacturing readiness and resiliency”, Sistu adds. These include, but are not limited to, digital twins, process modelling and production scheduling.
“Moving to the cloud allows for better interoperability between different business units by dissolving data silos,” Liautaud continues. “This offers on-demand scalability, which should then improve businesses’ decision-making, as manufacturers are able to react more quickly to any unexpected changes.”
According to an Accenture report published in June, supply chain executives credit the cloud with driving a 5% growth in revenue on average, a 16% decrease in operating costs, and a 26% improvement in demand forecasting accuracy.
Despite the perceived benefits, only 52% of the 1,050 supply chain executives surveyed said moving to the cloud had helped them to be more resilient, while just 41% achieved increased visibility as a result of their cloud investment.
While there should be no doubt that the cloud can play a pivotal role in helping manufacturers get the insights required to become more resilient, says Sistu, it can only really be realised if “architected as part of [an] edge cloud continuum”.
Edge computing – where data is no longer confined to data centres and is processed as close to the original source of data as possible – can help by reducing the latency between two points of a network. The problem, then, is that “manufacturing’s legacy systems can be a hindrance to the seamless data integration from edge to cloud”. This is thwarting some manufacturers’ efforts to transform themselves digitally, Sistu argues.
With multiple stakeholders in any single supply chain, the edge should ideally be deployed by all parties, whether upstream or downstream. Creating digital data threads would enable data to flow seamlessly between stakeholders, Sistu adds.
The Accenture research found that one in five of the supply chain executives surveyed had deployed cloud-enabled capabilities across their entire supply chain. Of these executives, 97% had at least three-quarters of their entire supply chains running in the cloud.
However, beyond the supply chain executives, overall two out of three respondents had less than half of their supply chain connected to the cloud. Companies that haven’t yet moved their supply chains to the cloud need to pick up the pace if they want to make themselves more resilient in the face of future disruptions, Accenture concluded.
“Ultimately, the biggest benefit of the cloud is that it can be the single source of truth, providing continuous global visibility into resources and supply chains,” says Sistu. “With this global visibility, manufacturers can forecast more effectively, optimise their production and drive workforce readiness. This puts them in a stronger position to be able to meet fluctuations in global supply and demand.”
And in a world where a small disruption on one side of the world can cause massive shockwaves and chaos on the other side, it’s worth doing whatever it takes to reinforce your supply chain.
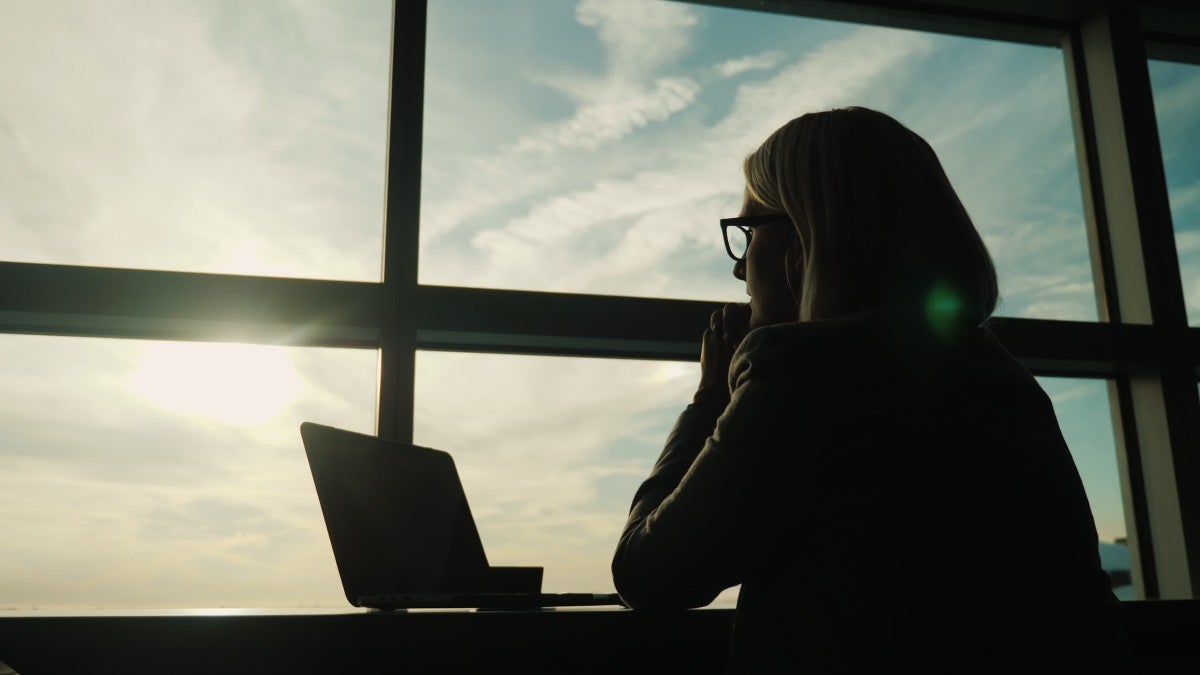
If the Covid-19 pandemic, geopolitical tensions and supply chain disruptions have taught manufacturers one thing, it’s to prepare for the unexpected. So, could cloud computing hold the key to resilience?
“The events of the past couple of years have put considerable pressure on the manufacturing sector to maintain production and keep supply chains and economies moving,” says Dr Phani Sistu, internet of things solutions lead at Hitachi Vantara, which offers storage solutions for businesses. “At the same time, manufacturers have had to deal with workforce challenges and supply and demand fluctuations.”
In pre-pandemic manufacturing conditions, just-in-time was the default model: a workflow system where parts are sourced as close to production as possible in order to meet customer demand without holding excess inventory.