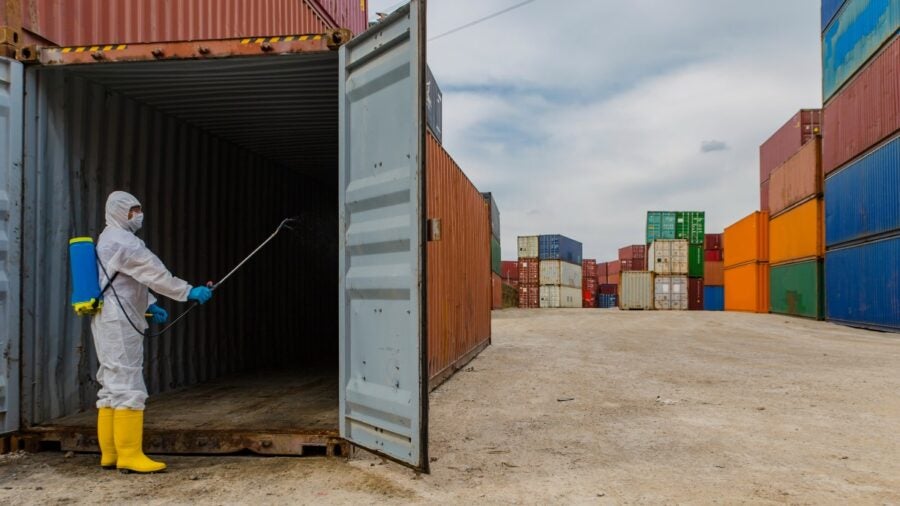
If you ask a group of purchasing chiefs about their experiences since 2020, you’ll find that few, if any, will look back with much fondness.
To say that the past three-plus years have been a challenge to the procurement profession would be a gross understatement. When Covid-19 started its deadly spread, the disruptions it triggered led to materials shortages around the world, causing input costs to spiral. This had a huge detrimental effect on manufacturing, resulting in a prolonged decline in output.
But the vice-like grip the crisis imposed on global supply chains is loosening at long last. In fact, several metrics suggest that we’re through the worst of it.
How is the outlook for procurement improving?
In May, global factories increased their output for the fourth consecutive month, while productivity in China recently hit an 11-month high after Beijing lifted Covid restrictions at the end of 2022. And, while manufacturing figures in the US dipped in June, they seemed to be stabilising in July, according to the Institute for Supply Management’s latest Purchasing Managers’ Index (PMI).
Among those surveyed for the PMI was a purchasing manager in the fabricated metal products sector who reported that supply chain conditions were returning to a situation broadly comparable to pre-pandemic conditions. Logistics costs had settled down, while transit times were getting shorter. Any remaining divergence was to be found in energy and raw materials costs.
Another purchasing manager, this time from the primary metals sector, noted that their order book was “strong”. And a respondent working in the food and beverages industry said that they expected production to increase soon, given the slight easing of inflation and an uptick in consumer confidence.
How are businesses boosting supply chain resilience?
Although the threat of recession still looms over several economies, things are undoubtedly starting to look healthier, and more familiar, for supply managers. Looking ahead, the key questions for professionals to consider are what lessons they’ve learnt since 2020; what changes the crisis has necessitated and whether corporate procurement teams are well enough prepared to handle the next big shock to the system.
Such questions are made more urgent by research findings suggesting that businesses are already reverting to old, short-termist habits. For instance, a survey by PwC in November 2022 found that 5% of senior executives in the US considered the task of increasing their firms’ responsiveness and resilience to be their highest priority in 2023. Only 23% included it as one of their top three priorities.
One company that’s clearly deemed the task vital is French electrical engineering firm Schneider Electric. It has been two years since the business adopted a supply chain strategy called “Strive” (standing for sustainability, trust, resilience, intelligence, velocity and efficiency). The firm’s main aim in doing so has been to make its supply chain more shock-resistant and customer-centred – and it seems to be succeeding. In May, Schneider topped Gartner’s rankings for the top 25 supply chains globally for the first time.
What has gone into this transformation? Kapila Mehta, vice-president for sustainability in the firm’s power products arm, explains that the forces at work during the pandemic (and events such as the semiconductor shortage) made the global market “increasingly dynamic and uncertain”. Schneider realised that the situation demanded an appropriately agile response, so it gave its procurement teams licence to do whatever it took to adapt quickly to changes in the market and so continue meeting customers’ needs in a timely fashion.
Now that things have calmed down a little, Schneider is working with thousands of its upstream partners to lock in vital supplies with the expectation that this will guarantee operational continuity. It has also committed to making full use of its network of 180-plus factories and nearly 90 distribution centres to ensure maximum flexibility and responsiveness.
Could digitisation and sustainability help with resilience?
Another important change over the past few years in procurement has been an increasing focus on two longer-term objectives: digitisation and sustainability. Schneider first set out to decarbonise its operations in 2019, for instance, pledging to cut its scope-three (supply chain) emissions by a quarter before 2030.
The sharp increase in fuel and energy costs caused by the war in Ukraine may have looked like a serious stumbling block to Schneider in its pursuit of this goal. But Mehta explains that the situation only underscored the need to digitise and electrify the firm’s supply chain operations to make improved energy efficiency and certain sustainability objectives more achievable.
Why onshoring and friendshoring are here to stay
Another way that some resilience-focused procurement teams have been safeguarding their operations is through multisourcing, whereby they use two or more suppliers to deliver the same item. The simple logic behind this practice is that drawing upon several sources in different locations should limit any disruption if a supplier at one site runs into problems.
Having multiple outsourced manufacturing sites across several regions, closer to end markets, can help to mitigate risk
Lynn Torrel is chief procurement and supply chain officer at electronics giant Flex, which found itself on the receiving end of much of the disruption to manufacturing during the Covid crisis. She points out that, while “single-location in-house production” may offer economies of scale, “having multiple outsourced manufacturing sites across several regions, closer to end markets, can help to mitigate risk”.
Torrel adds that the benefits of spreading the risk of disruption this way will, of course, need to be balanced against “the efficiency of your freight and logistics, which is dependent on your location”.
Comparable practices, such as friendshoring and onshoring, also look set to continue as long as geopolitical tensions remain high. But Mehta warns that these measures won’t be the ideal solution for all companies.
“There is a large movement towards localisation, but this needs to be driven by the pursuit of both resilience and sustainability,” she stresses.
Have companies really embraced supply chain flexibility?
If the events of the past three years have taught supply chain professionals anything, it’s that they have to be flexible to avoid getting caught out. “To be resilient enough to withstand disruption, businesses need the right mix of global and local supply chains,” Mehta argues.
Even a well-balanced hybrid approach of this type can never make a supply chain bulletproof, of course, but it will put a business in the best possible position to handle the next big shock around the corner.
As Torrel concludes: “Supply chain disruption is inevitable. Your biggest challenge is how effectively you can recover from it.”