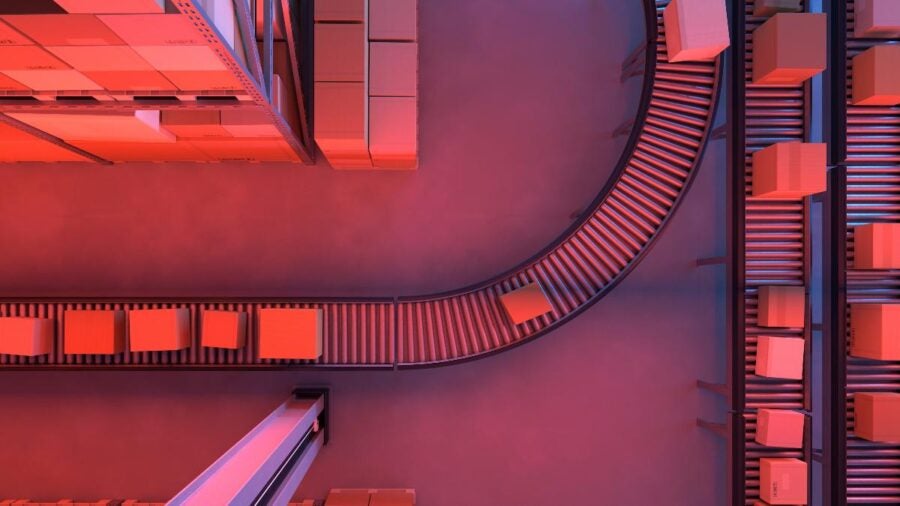
Walk into a meeting of supply chain managers and you might wonder whether you’ve stepped back in time several decades. According to research published in 2021 by Logistics UK, 89% of people working in this field are white and 83% are men.
Not only is the profession pale and male – it’s stale too. As more and more people in this ageing workforce retire, employers are struggling to find new blood to replace them. Recruitment giant Hays reports that more than three-quarters of employers seeking to hire into the supply chain and logistics sector this year are expecting a dearth of applicants.
There’s clearly a blockage in the talent pipeline, but why? And what can those in the industry do to clear it and so help to solve a chronic skills shortage?
Are supply chain jobs vulnerable to automation?
One of the key factors restricting the inflow is that procurement is often high on lists of roles at risk of being automated to extinction. After all, employers are bound to want to seize upon the efficiency savings offered by tech such as machine learning and robotics.
That, coupled with the recent slew of media reports highlighting failures in important supply chains and their ramifications, may well have deterred potential entrants to the field.
Scott Dance, a senior director specialising in procurement, logistics and supply chain management at Hays, believes that there’s a general lack of knowledge about the profession and its activities. An education campaign explaining how people in the business go about their work should help to reduce the fear factor.
AI is likely to replace certain responsibilities as opposed to entire roles
“One way to help close the skills gap is to encourage young professionals into the industry, but people’s limited understanding of what this sector does, and its growing importance, is a significant entry barrier to new talent,” he says. “We must raise awareness of what’s involved in supply chain management and why it’s such an appealing thing to be a part of.”
Dance suggests that telling good news stories about the profession – its integral role in sourcing parts for life-saving equipment such as radiotherapy machines, for instance – is one route.
“A good place to start is to ensure that careers advisers in schools and universities stress how crucial the supply chain sector is to everyday life and the UK economy – and how much potential there is for a fulfilling career in this industry,” he says.
Why it’s time to upgrade pay and conditions
Another useful measure would be to debunk some of the popular myths circulating about how recent technological developments could affect the sector.
“While the rise of generative AI has sparked concern about job security across the supply chain landscape, AI is likely to replace certain responsibilities as opposed to entire roles,” Dance predicts. “A lot of the manual and, arguably, mundane work can be automated, for instance, freeing up professionals to focus on more exciting projects.”
Jose Arturo Garza-Reyes is professor of operations management and head of the Centre for Supply Chain Improvement at the University of Derby. He notes that that sectors such as tourism, healthcare and IT have also faced severe skills shortages in recent years and have had to improve pay and conditions significantly to become more attractive career options.
If supply chain businesses don’t take similar action to close their skills gaps, the ramifications could be serious, adds Garza-Reyes, warning of “operational inefficiencies, delays and increased costs for both companies and consumers”.
Any failure to act decisively could also harm firms’ extant procurement teams, who in many cases have been struggling to keep things running smoothly while chronically understaffed.
“Since existing employees may have needed to take on extra responsibilities, their increased workload may cause burnout,” Garza-Reyes stresses. “Not tackling the skills shortage may result in heightened health and safety risks, as well as defective products and services. This can also disrupt supply chain operations, which would affect production, delivery and, ultimately, customer satisfaction.”
AI’s advance is a chance to learn new skills
Given such risks, embracing tech such as generative AI could, as long as the rationale is explained carefully, actually offer a solution to the skills shortage. One possible move might be training up people who have some familiarity with supply chains but may perhaps lack all the digital skills required in the sector.
Ambrozy Rybicki is co-founder and CEO of ARP Ideas, a software developer that also provides outsourced IT expertise. He stresses that “supply chain employers must recognise the importance of new IT skills in optimising their operations. Investing in continuous training programmes for employees can enhance their technical capabilities.”
While Rybicki admits that this may be easier said than done, he highlights the importance of tackling the problem promptly, rather than leaving it to fester.
“Developing in-house expertise requires time, resources and a clear understanding of emerging technologies,” Rybicki says. “But ignoring the widening tech skills gap will have detrimental effects on the supply chain industry. Companies may struggle to keep pace with technological advancements, leading to inefficiency, cost inflation and a loss of competitiveness.”
In the highly competitive field that supply chain management has become, that could be fatal.
“The inability to innovate and adapt to market demands may hinder growth and long-term success,” he says. “Whether through in-house development or strategic collaboration with IT experts, taking proactive steps to bridge the skills gap is vital for a resilient, agile and forward-looking supply chain industry.”
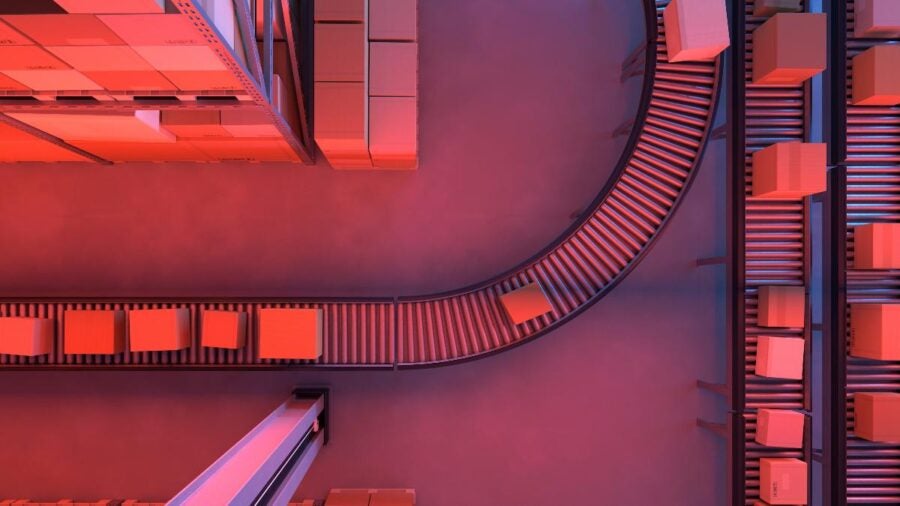
Walk into a meeting of supply chain managers and you might wonder whether you’ve stepped back in time several decades. According to research published in 2021 by Logistics UK, 89% of people working in this field are white and 83% are men.
Not only is the profession pale and male – it’s stale too. As more and more people in this ageing workforce retire, employers are struggling to find new blood to replace them. Recruitment giant Hays reports that more than three-quarters of employers seeking to hire into the supply chain and logistics sector this year are expecting a dearth of applicants.
There’s clearly a blockage in the talent pipeline, but why? And what can those in the industry do to clear it and so help to solve a chronic skills shortage?