01 Digital twins
Construction remains a decentralised industry, with overlapping and inefficient interfaces between design, construction and operation. A digital twin provides a virtual representation of physical assets and/or projects, including all the information from design through construction to operation. By connecting plans, engineering, geographical and other data, these separate data silos can be managed in an integrated way, transforming construction.
The digital twin can analyse all the incoming data and use it for continuous improvement in delivery. This can provide big benefits in terms of responding to changes, improving operations and adding value. They can be used for construction, buildings and plant management, even smart cities deployment.
In the UK, a digital twin was implemented for Thames Estuary flood management, which had 70 years of historical data in a variety of formats. By ensuring seamless access to previously hidden information for thirty offices across ten organisations, the project achieved 25 per cent faster data retrieval, and transformed the way different agencies, developers and designers work together.
02 Drones
Unmanned aerial vehicles, or drones, have wide applications in construction pre, during and post-build. Ground surveys are a common reason for delays, when undetected geological elements are discovered on site. As Nick Sacke, at Comms365, says: “Light detection and ranging (lidar), combined with ground-penetrating radar and GPS positioning, provides additional data allowing for more detailed surveying of above and below groundwork before construction begins.”
In addition, drone use can impact workforce safety. During construction, it is far safer to access hard-to-reach or dangerous areas without the corresponding health and safety risks of inspection by an individual. They can also be used to map changes in the project, keeping track of any real-time errors in construction, which can be fed back into a digital twin.
Best of all, they can be built into ongoing operations and maintenance. For example, with the King Abdullah Financial District Metro Hub in Riyadh, Saudi Arabia, Newtecnic engineered the project so inspection, monitoring and precise measurement of normally concealed areas, behind panels and within the completed building’s fabric, are executed by small flying lidar and camera-equipped drones and robots.
03 DfMA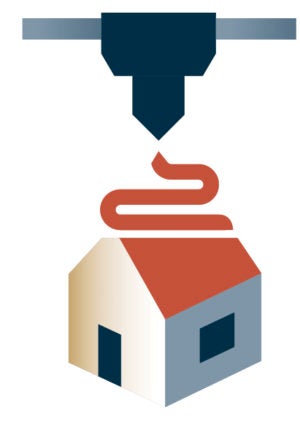
The idea of engineering a project to enable drone-based maintenance leads us on to design for manufacture and assembly or DfMA. While many industries have adopted technology to increase personalisation and customisation to drive markets, this is a relatively new development in construction.
What DfMA requires is that the design process results in objects and/or materials that are easy to both manufacture or assemble. This can be modular design, the use of 3D printing or even local construction labs, enabling parts and replacements to be manufactured to specification on site.
As Andrew Watts, chief executive of Newtenic, says: “The introduction of digital technology makes construction as efficient as any advanced manufacturing process where precise component quantities are made to order. Because these have assured quality and exacting specifications, based on the as-built construction, they are guaranteed to match the structure and have predictable performance over a pre-determined life cycle. Additional value is produced because, as in a modern mass-customisation car factory, every part is accounted for and there is no waste.”
04 Augmented reality
The thing about augmented reality (AR) is that it means a partially rendered environment, not a fully virtual one. While a virtual reality experience may be useful to show potential investors what something might look like in the future, AR provides an overlay to views of the real world. This means information on detailing tasks, safety alerts and other support can be provided to what workers are seeing on tablets or through smartglasses and even hard hats.
As Mr Sacke, of Comms365, points out: “AR could be used to position holographic markings displaying warnings and awareness of an electrical conduit, which is positioned behind a wall, to caution and inform engineers who would be accessing this area of the building in the future.”
It’s not just on-site safety and management though. As James Woodall, co-founder and chief technology officer at Intoware, says: “Away from the site, data-visualisation tools can use this wealth of information to identify bottlenecks and problems that simply can’t be captured on paper. From a business point of view, the use of wearable digital work instruction products improves speed, accuracy and convenience, which all ultimately contribute to the bottom line.”
05 New materials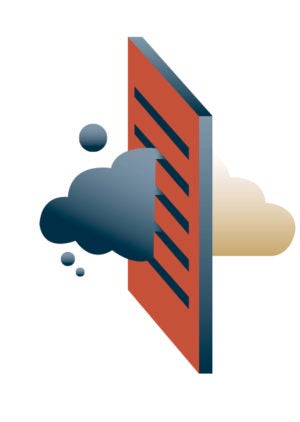
Development of new materials is a necessity for many industries, with increasing demand for low-carbon and sustainable operations. A Nasa offshoot, PURETi, is transforming the building façade sintered stone market through its partnership with Neolith. PURETi has developed a photocatalytic surface which eats pollution; it literally cleans the air around it.
Using a liquid form of titanium dioxide and its natural reaction to ultraviolet light, the material can remove free radicals and other pollutants from surfaces, air and water. This means it transforms Neolith sintered stone façades into self-cleaning air purifiers, consequently reversing pollution, dramatically improving air quality and enabling the slabs to stay cleaner for longer.
While this is a huge societal benefit, it also means that treated sections of the façade keep surfaces clean, an extra benefit for the building owner. As Lauren Underwood, senior research scientist at Stennis Space Center, Mississippi, who worked on the original Nasa project says: “It’s exciting that there is a non-toxic mechanism to keep buildings clean and at the same time reduce maintenance, energy costs and the use of harsh chemicals.”
06 Back to basics
When we talk about innovation, the assumption is often that we’re talking computing-based breakthroughs, imagined in sterile, clean laboratories with little connection to the natural world. Yet one of the most exciting recent breakthroughs in construction is the discovery that bricks can be made of human urine.
Researchers in South Africa at the University of Cape Town have developed a zero-waste building material made with urine, as an alternative to kiln-fired bricks. Regular bricks are fired at temperatures around 400C and produce vast quantities of carbon dioxide, while bio-bricks are made in moulds at room temperature.
To create the bricks, urine, loose sand and a bacteria that produces the enzyme urease are combined in a brick-shaped mould. The urease triggers a chemical reaction, breaking down the urea in urine, while producing calcium carbonate, also known as limestone, the main component of cement. The bio-brick process creates nitrogen and potassium, useful for fertiliser, as by-products and means the process is ultimately zero waste with 100 per cent of the urine converted into something useful.
07 Robots
For many of us, robotics are a thing of fiction and film, as when Ripley used a robot exoskeleton to fight the xenomorph queen in Aliens. They are already in use today though, in a range of sizes and niches. Willmot Dixon is currently trialling Eksovest, a robotic exoskeleton vest to help protect the human form. The idea is that it should assist in lifting items and performing repetitive overhead tasks.
Advanced Construction Robotics is using its TyBot to tie steel reinforcement bars for building projects, while the small Q-Bot is helping to retrofit buildings through applying insulating materials in the spaces between floorboards and foundations.
But the next big thing is swarm robotics. Spain’s Institute for Advanced Architecture of Catalonia is creating its own swarm of structure building robots. These “mini-builders” are like small 3D printers depositing material in layers, connected to a central vat. While the swarm model is very new, it is developing fast. Assistant Professor Pham Quang Cuong, at Nanyang Technological University, Singapore, is already working on the next stage, developing better mobility planning to enable the swarms to operate in rougher environments, which is exactly what construction needs.